$14.57 Billion Expanding Demand for Servo Motor Market in the U.S., China, and Germany by 2025
Discover comprehensive insights into the global servo motor industry, exploring upstream and downstream components, market trends, manufacturing challenges, and technological innovations. Learn about various servo motor types, their applications in robotics and automation, and regional market dynamics across the US, China, and Germany. Understand the impact of AI integration, sustainability initiatives, and competitive landscape shaping the future of servo motor technology.
- Last Updated:
Servo Motor Market Q1 and Q2 2025 Forecast
The Servo Motor market, with a projected size of $14.57 billion in 2025, is anticipated to grow at a CAGR of 5.82% from 2025 to 2033. In Q1 2025, the market is expected to generate approximately $3.6 billion, as industries like automotive, electronics, and robotics continue to demand more precise control and performance. The U.S., China, and Germany remain key markets, with servo motors being crucial to automation, robotics, and advanced manufacturing systems.
By Q2 2025, the market is predicted to reach $3.75 billion, as industrial automation and robotics applications proliferate across China and Germany, spurring growth. The demand for smart factories and Industry 4.0 technologies will continue to be a major driver for the servo motor market.
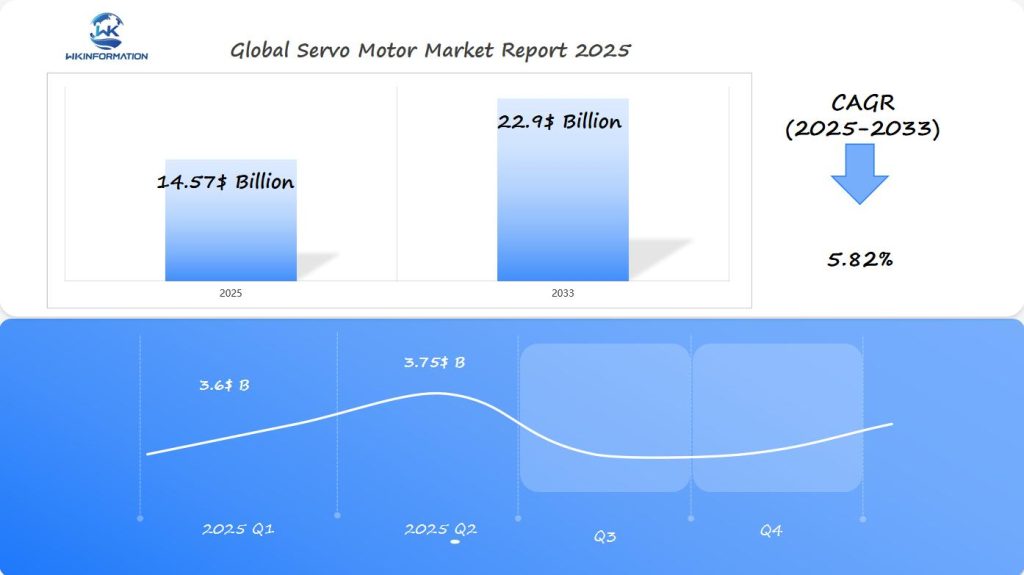
Exploring the Global Servo Motor Upstream and Downstream Industry Chains
The servo motor industry chain operates through a complex network of suppliers, manufacturers, and end-users. Understanding these connections helps businesses optimize their operations and maintain competitive advantages.
Upstream Components
- Raw Materials Suppliers: Copper, steel, aluminum, and rare earth magnets
- Electronic Component Manufacturers: Circuit boards, semiconductors, encoders
- Precision Parts Producers: Bearings, gears, shafts
Downstream Components
- Assembly Plants: Integration of components into finished servo motors
- Distribution Networks: Warehousing and logistics services
- End-User Industries: Robotics, manufacturing, aerospace
Key players like ABB and Siemens AG maintain strong relationships with suppliers to ensure consistent material quality and timely deliveries. These manufacturers often implement vertical integration strategies, controlling multiple stages of production to reduce dependencies on external suppliers.
Supply chain efficiency directly impacts market performance through:
- Reduced production costs
- Faster time-to-market
- Enhanced quality control
- Better inventory management
Recent disruptions have prompted companies to adopt digital supply chain solutions and establish regional manufacturing hubs. This shift helps minimize risks and ensures steady production flow, particularly crucial in high-demand markets like China, the U.S., and Germany.
Key Trends in the Servo Motor Market: Automation and Precision Control
The manufacturing sector’s rapid shift toward automation has created unprecedented demand for servo motors. Industries ranging from automotive production to packaging now rely on these precision devices to achieve higher production rates and maintain consistent quality standards.
1. Automation Driving Growth
- Smart factories implement servo motors in robotic arms, conveyor systems, and assembly lines
- Food and beverage industry adoption rates increased 45% in 2022
- Pharmaceutical manufacturing uses servo-driven systems for precise medication dosing
2. Precision Requirements
Modern manufacturing tolerances demand exceptional accuracy levels:
- Semiconductor production: ±0.001mm positioning accuracy
- 3D printing applications: Layer precision of 0.1mm or less
- Medical device assembly: Microscopic component placement
3. Emerging Technology Integration
The servo motor landscape continues to evolve with new technological capabilities:
- IoT IntegrationReal-time performance monitoring
- Predictive maintenance alerts
- Remote operation capabilities
- Miniaturization AdvancesCompact designs for mobile robotics
- Reduced power consumption
- Enhanced power-to-size ratios
- Smart FeaturesSelf-diagnostic capabilities
- Adaptive control systems
- Energy optimization algorithms
The industrial automation wave has pushed servo motor manufacturers to develop increasingly sophisticated solutions. These innovations enable manufacturers to meet strict quality standards while maintaining high production volumes.
Challenges in Servo Motor Manufacturing: Cost, Efficiency, and Innovation
Servo motor manufacturers face significant hurdles in meeting market demands while maintaining profitability. Raw material costs, particularly for rare earth magnets and high-grade copper windings, create substantial pressure on production budgets. These essential components can represent up to 40% of the total manufacturing costs.
Key Manufacturing Challenges:
- Complex assembly processes requiring specialized equipment
- High-precision requirements leading to increased quality control costs
- Rising labor expenses in traditional manufacturing hubs
- Supply chain volatility affecting component availability
The push for advanced features creates additional strain on manufacturers. Modern servo motors must integrate:
- Smart diagnostics capabilities
- Enhanced energy efficiency
- Compact designs
- Improved thermal management
Innovation vs. Cost Balance:
The market demands cutting-edge features at competitive prices. Manufacturers invest heavily in R&D while seeking cost-effective solutions through:
- Automated production lines
- Alternative material exploration
- Design optimization
- Lean manufacturing practices
Manufacturing Solutions:
Successful companies implement strategic approaches:
- Investment in advanced robotics for precision assembly
- Development of modular designs to streamline production
- Implementation of predictive maintenance systems
- Adoption of digital twin technology for testing
These manufacturing challenges drive continuous innovation in production methods. Companies exploring composite materials and advanced manufacturing techniques position themselves to meet evolving market demands while maintaining competitive pricing structures.
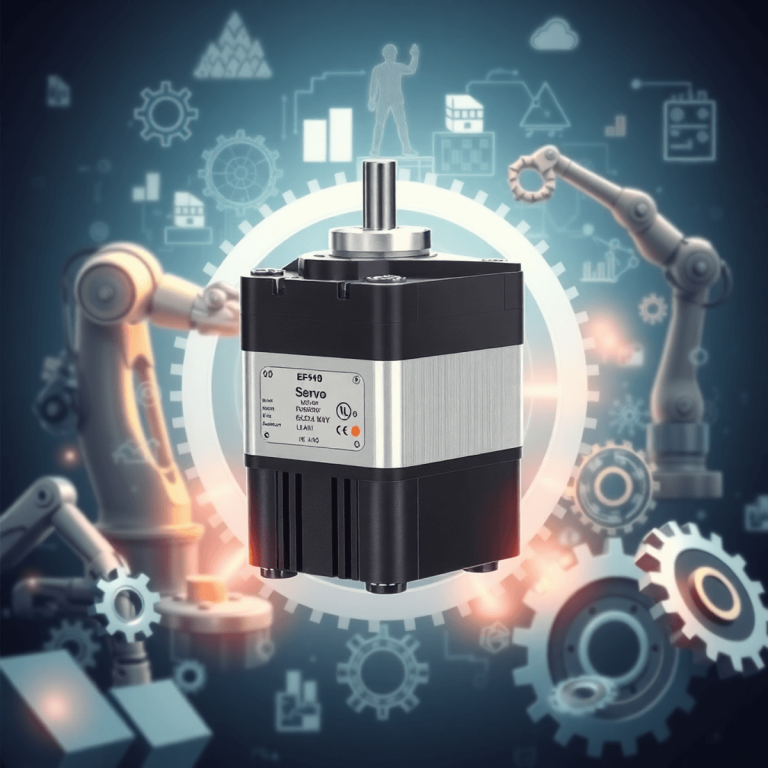
Geopolitical Impact on the Servo Motor Industry and Global Trade
The servo motor industry faces significant challenges due to shifting geopolitical dynamics. Trade tensions between major economies create ripple effects across the global supply chain, impacting production costs and market accessibility.
Key Trade Regulation Impacts:
- Import tariffs ranging from 5% to 25% on servo motors
- Export restrictions on advanced motor technologies
- Varying certification requirements across regions
- Complex customs clearance procedures
Recent trade disputes between the U.S. and China have reshaped supply chain strategies. Chinese manufacturers now focus on developing domestic alternatives, while U.S. companies explore production facilities in countries like Vietnam and Mexico.
Regional Market Access Variations:
- EU benefits from standardized regulations across member states
- ASEAN countries enjoy reduced tariffs through free trade agreements
- North American markets leverage USMCA advantages
- Middle Eastern markets face higher entry barriers due to regional regulations
Intellectual property protection remains a critical concern, particularly for manufacturers operating in emerging markets. Companies must navigate complex patent laws and technology transfer restrictions while maintaining competitive advantages.
The semiconductor shortage has intensified regional competition, with countries implementing protective measures for critical components. This has led to increased stockpiling behaviors and the emergence of parallel supply chains, affecting servo motor production schedules and costs.
Types of Servo Motors: AC, DC, and Brushless Motors
The servo motor market features three distinct technologies, each with unique characteristics suited for specific applications:
1. AC Servo Motors
- High torque output at variable speeds
- Superior performance in high-speed applications
- Excellent acceleration and deceleration control
- Larger size and higher initial cost
- Ideal for industrial machinery and robotics
2. DC Servo Motors
- Cost-effective solution for basic applications
- Simple control mechanisms
- Quick response time
- Limited speed range
- Requires regular maintenance due to brush wear
- Best suited for small-scale automation
3. Brushless DC Motors
- Combines advantages of both AC and DC technologies
- Enhanced efficiency up to 90%
- Minimal maintenance requirements
- Extended operational lifespan
- Compact design with high power density
- Precise speed control capabilities
The rise of brushless technology marks a significant shift in servo motor applications. These motors eliminate the need for mechanical commutation, reducing wear and maintenance while delivering superior performance. Industries ranging from medical equipment to aerospace increasingly favor brushless designs for their reliability and compact form factor.
Recent advancements in brushless motor design have introduced smart features like integrated position sensors and advanced thermal management systems. These innovations enable real-time monitoring and enhanced operational efficiency, making brushless motors the preferred choice for modern automation systems.
Applications of Servo Motors in Robotics, Automation, and Manufacturing
Servo motors power critical operations across multiple industrial sectors, delivering precise control and reliable performance in demanding applications.
Robotics Applications:
- Robotic arms utilize servo motors for exact positioning and smooth movement control
- Delta robots in pick-and-place operations achieve high-speed accuracy through servo motor systems
- Collaborative robots (cobots) depend on servo motors for safe human-robot interactions
Industrial Automation:
- Conveyor systems employ servo motors for variable speed control and positioning
- Packaging machines achieve precise product handling and wrapping
- Textile manufacturing equipment maintains consistent tension and speed control
Manufacturing Processes:
- CNC machines rely on servo motors for:
- Tool positioning
- Workpiece manipulation
- Axis control
- 3D printers use servo motors for precise layer deposition
- Assembly lines integrate servo systems for synchronized operations
Specialized Applications:
- Medical equipment requires servo motors for precise instrument control
- Semiconductor manufacturing demands ultra-precise positioning
- Food processing equipment uses servo motors for portion control and cutting operations
The versatility of servo motors enables manufacturers to achieve:
- Reduced production time
- Improved product quality
- Enhanced operational efficiency
- Decreased waste
- Better energy management
These applications demonstrate servo motors’ essential role in modern industrial processes, driving innovation and productivity improvements across diverse sectors.
Global Insights into the Servo Motor Market
The servo motor market shows different characteristics in different regions, influenced by local industrial needs and technological abilities. Analyzing the market reveals several important trends:
1. Regional Market Distribution
- Asia-Pacific: 45% market share
- North America: 28% market share
- Europe: 20% market share
- Rest of World: 7% market share
2. Key Growth Drivers
- Rising industrial automation adoption rates
- Increasing demand for precision manufacturing
- Growing investment in smart manufacturing facilities
- Expansion of electronics and semiconductor industries
The market shows strong segmentation based on power output:
- Low-power servo motors (< 1kW): Dominate consumer electronics
- Medium-power servo motors (1-5kW): Lead in industrial automation
- High-power servo motors (> 5kW): Essential in heavy machinery
Recent market data indicates a shift toward energy-efficient servo motors, with manufacturers reporting a 30% increase in demand for eco-friendly variants. The integration of predictive maintenance capabilities has become a standard feature, reducing downtime by up to 40% in industrial applications.
Industry experts project sustained growth in emerging markets, particularly in Southeast Asia and Latin America, where manufacturing sectors are rapidly modernizing their infrastructure.
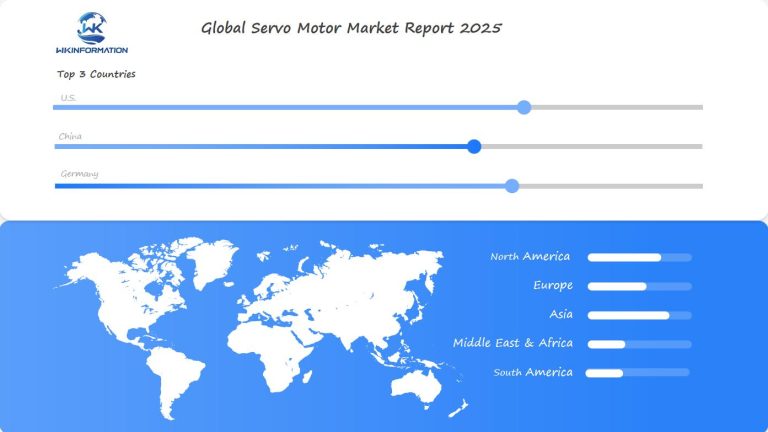
U.S. Servo Motor Market: Demand from Robotics and Aerospace
The U.S. servo motor market is experiencing strong growth due to significant investments in robotics and aerospace applications. American manufacturers are using advanced servo systems in robotic assembly lines, automated warehouses, and precise manufacturing processes.
Key Growth Drivers in the U.S. Market:
1. Aerospace Applications
- Flight control systems
- Landing gear mechanisms
- Satellite positioning equipment
- Aircraft manufacturing automation
2. Robotics Integration
- Collaborative robots in manufacturing
- Automated guided vehicles (AGVs)
- Pick-and-place operations
- Quality control systems
The defense sector is crucial for the U.S. servo motor market, with increasing demand for high-precision motors in military applications. These specialized motors must meet strict military specifications for reliability and performance in extreme conditions.
Silicon Valley startups are pushing boundaries of innovation by creating smart servo motors with improved connectivity features. These next-generation motors include advanced sensors and real-time monitoring capabilities, fulfilling the requirements of Industry 4.0 initiatives.
U.S. manufacturers such as Rockwell Automation and Parker Hannifin are heavily investing in research and development to create servo motors with better power density and efficiency. Their focus on miniaturization addresses the rising need for compact, high-performance solutions in medical robotics and semiconductor manufacturing equipment.
The market is particularly strong in states with concentrated manufacturing hubs like Michigan, California, and Texas, where the automotive and technology sectors consistently drive demand for precise motion control solutions.
China’s Servo Motor Market: Growth in Manufacturing and Automation
China’s servo motor market is experiencing significant growth, driven by the country’s ambitious Made in China 2025 initiative. The transformation of the domestic manufacturing sector has created an unprecedented demand for high-precision automation equipment.
Key growth indicators in China’s servo motor market:
- Annual production capacity: 500,000+ units
- Market share: 35% of global servo motor production
- Growth rate: 8.2% year-over-year
Local manufacturers like Estun Automation and GSK CNC Equipment have emerged as significant players, challenging traditional international brands. These companies offer cost-competitive alternatives while maintaining quality standards comparable to international competitors.
Distinct preferences in the Chinese market
The Chinese market shows distinct preferences:
- Mid-range servo motors for general automation
- High-precision units for semiconductor manufacturing
- Compact designs for mobile robotics
Recent investments in smart manufacturing hubs across Shanghai, Shenzhen, and Guangzhou have accelerated servo motor adoption. These manufacturing centers specifically focus on:
- Advanced electronics production
- Electric vehicle assembly lines
- Automated packaging systems
- Smart warehouse operations
Chinese manufacturers are rapidly advancing their technological capabilities, with many now producing servo motors featuring integrated diagnostic systems and predictive maintenance capabilities. This technological evolution positions China as a crucial player in the global servo motor supply chain.
Germany’s Servo Motor Market: Precision Engineering and Industry 4.0
Germany’s servo motor market is a shining example of the country’s engineering excellence, especially in its application of Industry 4.0 principles. The German market has distinct features shaped by its strong manufacturing industry and dedication to technological innovation.
Key Market Drivers:
- Integration of smart manufacturing solutions
- High demand for precision engineering applications
- Strong presence of automotive and machinery manufacturers
- Investment in research and development initiatives
German manufacturers have established themselves as leaders in high-precision servo motor applications, with companies like Siemens and Bosch Rexroth setting industry standards. These companies leverage advanced manufacturing techniques and quality control processes to produce servo motors with exceptional accuracy and reliability.
The adoption of Industry 4.0 practices has created new opportunities in the German servo motor market:
- Digital Twin Technology: Implementation of virtual modeling for servo motor systems
- Predictive Maintenance: Integration of sensors for real-time performance monitoring
- Smart Factory Solutions: Automated production lines with interconnected servo systems
- Energy Efficiency: Development of eco-friendly servo motor designs
German manufacturers focus on specialized applications requiring ultra-precise motion control, such as semiconductor manufacturing equipment and medical devices. This specialization has positioned Germany as a preferred supplier for high-end servo motor solutions in the global market.
The market benefits from strong government support through initiatives like the High-Tech Strategy 2025, which promotes technological innovation and digital transformation in manufacturing sectors.
The Future of Servo Motors: AI Integration and Efficiency Enhancements
AI Integration: Transforming Servo Motor Technology
AI integration is set to transform the servo motor industry by introducing advanced predictive maintenance systems and self-optimizing capabilities. Machine learning algorithms will play a crucial role in this transformation, as they will analyze real-time performance data and automatically adjust motor parameters for optimal operation.
These intelligent systems will have the ability to:
- Detect potential failures before they happen
- Optimize energy consumption patterns
- Adjust torque and speed settings based on load variations
- Self-calibrate for maximum precision
Technological Advancements in Efficiency
In addition to AI integration, there are several technological advancements that are expected to enhance the efficiency of servo motors.
New winding techniques are being developed that can reduce energy losses by up to 30% compared to traditional designs. These techniques involve using different methods of winding the wire around the motor’s core, which can result in less energy being wasted as heat.
Advanced materials such as high-performance magnets and innovative core compositions are also being used to improve power density while minimizing heat generation. By using these materials, manufacturers can create smaller and lighter servo motors that still deliver the same amount of power.
Key Efficiency Improvements:
- Nano-engineered magnetic materials
- Advanced thermal management systems
- High-density copper windings
- Smart cooling solutions
Sustainability Focus in Servo Motor Development
Another important trend in the future of servo motors is the focus on sustainability. As concerns about climate change and environmental impact grow, manufacturers are increasingly looking for ways to make their products more eco-friendly.
Some of the initiatives being implemented include:
- Using recyclable components in motor construction
- Incorporating energy-regenerative braking systems that capture and store energy during deceleration
- Utilizing bio-based insulation materials instead of traditional petroleum-based ones
- Implementing zero-waste manufacturing processes where all byproducts are reused or recycled
Digital Twin Technology: Streamlining Design Processes
Digital twin technology is another area that holds promise for the future of servo motors. This technology allows engineers to create virtual replicas (or “twins”) of physical objects or systems, which can then be used for testing and optimization purposes.
By creating digital twins of servo motor designs, manufacturers can identify potential issues or areas for improvement before actually producing any physical prototypes. This not only saves time but also reduces costs associated with trial-and-error approaches.
Smart Sensors: Enabling Real-Time Monitoring
Smart sensors are becoming increasingly common in various industries, including manufacturing. These sensors are capable of collecting large amounts of data about a system’s performance and transmitting it wirelessly to a central hub or cloud platform.
In the context of servo motors, smart sensors can provide continuous monitoring of key parameters such as temperature, vibration, and current draw. This data can then be used for predictive maintenance purposes – identifying when a motor is likely to fail based on historical patterns rather than waiting for it to break down completely.
Edge Computing: Enhancing Responsiveness
As mentioned earlier, response time is critical in many applications where servo motors are used (e.g., robotics). One way to improve response times is through edge computing – a distributed computing model where data processing occurs closer to the source rather than relying solely on centralized servers.
By implementing edge computing capabilities within servo systems, manufacturers can achieve faster decision-making and reduced latency during operation. This means that actions such as adjusting speed or position based on feedback from sensors can happen almost instantaneously – leading to smoother motion control and better overall performance.
Competitive Landscape in the Servo Motor Industry
The servo motor industry has several major players who influence the market through strategic actions and technological advancements.
Key Market Leaders
-
Yaskawa Electric Corporation – Japan
-
ABB Ltd. – Switzerland
-
Siemens AG – Germany
-
Rockwell Automation Inc. – United States
-
Delta Electronics Inc. – Taiwan
-
Maxon Precision Motors Inc. – Switzerland
-
Mitsubishi Electric Corp. – Japan
-
FANUC Corp. – Japan
-
SANMOTION R. – Japan
-
Schneider Electric – France
Overall
Report Metric | Details |
---|---|
Report Name | Global Servo Motor Market Report |
Base Year | 2024 |
Segment by Type |
|
Segment by Application |
|
Geographies Covered |
|
Forecast units | USD million in value |
Report coverage | Revenue and volume forecast, company share, competitive landscape, growth factors and trends |
The servo motor market is projected to grow to $14.57 billion by 2025, highlighting its importance in industrial automation and technological progress. This growth is driven by:
- Increasing automation demands across manufacturing sectors
- Integration of AI and IoT technologies
- Rising need for precision control in advanced applications
- Growing focus on energy efficiency
Regional Growth Patterns
Key regional markets show different growth trends:
- United States: Leading innovation in robotics and aerospace applications
- China: Rapid expansion in manufacturing automation
- Germany: Pioneering Industry 4.0 implementations
Factors Influencing Market Evolution
The market’s development is influenced by technological advancements and competitive factors:
- Development of smart, connected servo systems
- Enhanced efficiency through AI-driven controls
- Strategic mergers and acquisitions among major players
- Focus on sustainable manufacturing practices
The servo motor industry is at a crucial point where traditional mechanical expertise combines with digital transformation. Companies that successfully integrate precision engineering with intelligent technologies will gain a significant market share in this growing sector. The industry’s growth trajectory indicates a future where servo motors have an increasingly vital role in shaping modern manufacturing and automation landscapes.
Global Servo Motor Market Report(Can Read by Free sample)–Table of Contents
Chapter 1:Servo Motor Market Analysis Overview
- Competitive Forces Analysis(Porter’s Five Forces)
- Strategic Growth Assessment(Ansoff Matrix)
- Industry Value Chain Insights
- Regional Trends and Key Market Drivers
- Servo Motor Market Segmentation Overview
Chapter 2:Competitive Landscape
- GlobalServo Motor Players and Regional Insights
- Key Players and Market Share Analysis
- Sales Trends of Leading Companies
- Year-on-Year Performance Insights
- Competitive Strategies and Market Positioning
- Key Differentiators and Strategic Moves
Chapter 3:Servo Motor Market Segmentation Analysis
- Key Data and Visual Insights
- Trends,Growth Rates,and Drivers
- Segment Dynamics and Insights
- Detailed Market Analysis by Segment
Chapter 4:Regional Market Performance
- Consumer Trends by Region
- Historical Data and Growth Forecasts
- Regional Growth Factors
- Economic,Demographic,and Technological Impacts
- Challenges and Opportunities in Key Regions
- Regional Trends and Market Shifts
- Key Cities and High-Demand Areas
Chapter 5:Servo Motor Emerging and Untapped Markets
- Growth Potential in Secondary Regions
- Trends,Challenges,and Opportunities
Chapter 6:Product and Application Segmentation
- Product Types and Innovation Trends
- Application-Based Market Insights
Chapter 7:Servo Motor Consumer Insights
- Demographics and Buying Behaviors
- TargetAudience Profiles
Chapter 8:Key Findings and Recommendations
- Summary of Servo Motor Market Insights
- Actionable Recommendations for Stakeholders
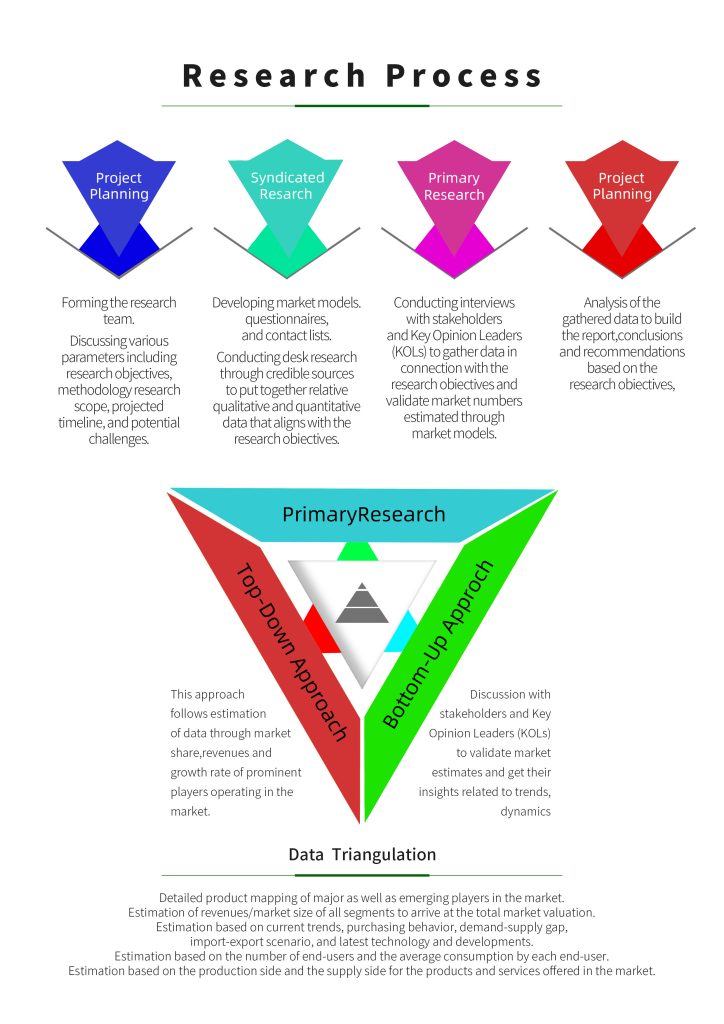
Access the study in MULTIPLEFORMATS
Didn’t find what you’re looking for?
TALK TO OUR ANALYST TEAM
Need something within your budget?
NO WORRIES! WE GOT YOU COVERED!
Call us on: +1-866-739-3133
Email: infor@wkinformation.com
What are the upstream and downstream components in the servo motor market?
The upstream components of the servo motor market include raw materials and parts suppliers, while downstream components involve distributors, retailers, and end-users. Together, these elements form a comprehensive supply chain that ensures the efficient production and distribution of servo motors.
How is automation driving the demand for servo motors?
The growing need for automation across various sectors, including manufacturing, has led to increased adoption of servo motors. These motors provide precision control and reliability, making them essential for modern automated systems.
What challenges do manufacturers face in producing high-quality servo motors?
Manufacturers encounter several challenges such as balancing cost with innovation, maintaining efficiency while meeting performance requirements, and addressing customer demands for advanced features without compromising affordability.
How do geopolitical factors impact the global trade of servo motors?
Geopolitical tensions can significantly influence trade regulations for servo motors, leading to varying barriers or opportunities in different regions. Favorable trade agreements may benefit certain markets while others may face restrictions based on political relationships.
What types of servo motors are commonly used in various applications?
The most common types of servo motors include AC motors, DC motors, and brushless motors. Each type has its advantages and disadvantages; for example, brushless motors are gaining popularity due to their improved efficiency and reliability compared to traditional brushed designs.
What future trends are expected to shape the servo motor industry?
Future trends include AI integration for adaptive control algorithms that enhance performance based on real-time feedback, as well as a focus on sustainability and efficiency improvements through technological advancements like new winding techniques that reduce operational losses.