$37.88 Billion Growing Refractory Market in the U.S., India, and China by 2025
Explore the dynamic growth of the refractory market across the U.S., India, and China, projected to reach $37.88 billion by 2025. Discover key market drivers, technological innovations, and industry challenges shaping this vital sector, with insights into sustainable practices and competitive landscape analysis.
- Last Updated:
Refractory Market Q1 and Q2 2025 Forecast
The Refractory market is expected to reach $37.88 billion in 2025, with a CAGR of 6.3% from 2025 to 2033. In Q1 2025, the market is projected to generate approximately $9.4 billion, driven by the ongoing demand for refractory products in industries such as steel production, cement manufacturing, and glass production in the U.S., India, and China. The increasing focus on energy-efficient production and sustainable practices is expected to drive the market’s growth.
By Q2 2025, the market is forecasted to reach $9.6 billion, supported by the rising demand for high-performance refractory materials in high-temperature processes across various industrial sectors. The U.S. leads in advanced refractory technologies, while China remains a key player in steel production, and India continues to see growth in industrial manufacturing.
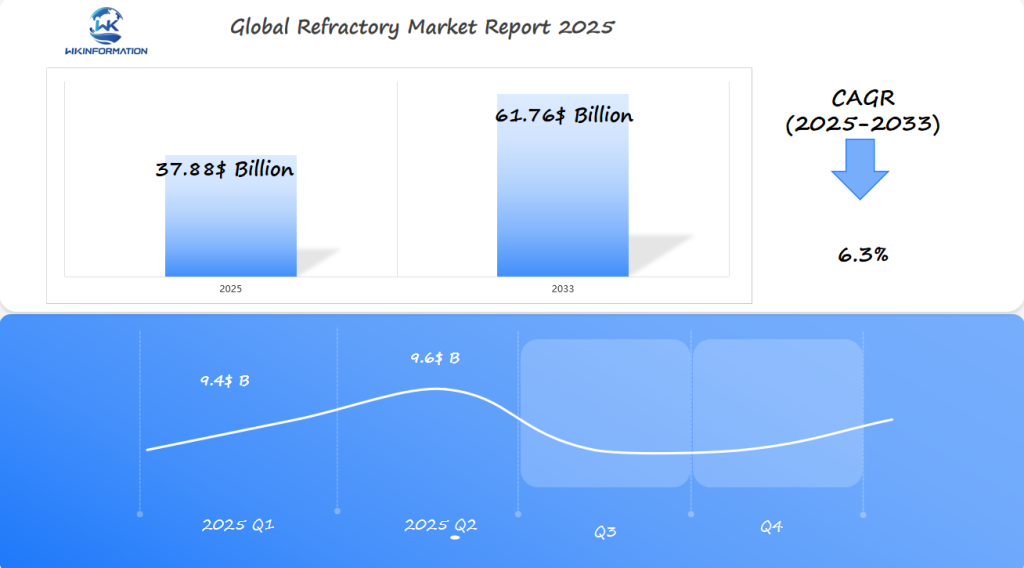
Understanding the Upstream and Downstream Activities of the Refractory Industry
The refractory industry has a complicated system of activities that work together, known as upstream and downstream activities. These activities create a lively supply chain ecosystem.
Upstream Activities
Upstream activities involve the processes that occur before the manufacturing stage. They include:
- Raw Material Mining: This involves the extraction of various minerals used in refractory production, such as:
- Bauxite
- Clay
- Magnesite
- Silica sand
- Material Processing: Once the raw materials are mined, they undergo various processes to prepare them for use in manufacturing. These processes include:
- Crushing and grinding
- Chemical treatment
- Quality control testing
- Raw material blending
Downstream Applications
Downstream activities refer to the applications and industries that utilize refractory products. These include:
- Primary Manufacturing: This involves the production of different types of refractories, such as:
- Shaped refractories
- Monolithic materials
- Specialized coatings
- Industrial Usage: Refractory products are used in various industries for specific applications, including:
- Steel furnace linings
- Cement kiln installations
- Glass melting tanks
- Petrochemical reactor vessels
The interconnectedness between these sectors creates a ripple effect throughout the supply chain. For example, if there is a price increase in raw material mining, it will directly impact manufacturing costs. Similarly, changes in industrial demand can influence mining operations.
This interdependence also extends to other aspects of the supply chain, such as transportation networks, storage facilities, and quality control systems.
Strategic Relationships in the Supply Chain
To ensure a consistent supply of quality materials, raw material suppliers maintain strategic relationships with manufacturers. These manufacturers, in turn, collaborate closely with end-users to develop customized refractory solutions for specific industrial applications.
The success of each sector relies on efficient coordination and communication across the entire supply chain network.
Key Trends Driving the Refractory Market Forward
The refractory market’s projected 6.0% CAGR through 2032 stems from several transformative trends reshaping the industry landscape:
1. Technological Innovation
- Advanced manufacturing processes incorporating AI and automation
- Smart sensors for real-time monitoring of refractory wear
- Development of nano-engineered refractory materials
- Implementation of predictive maintenance systems
2. Industrial Evolution
- Rapid expansion of electric arc furnaces in steelmaking
- Integration of Industry 4.0 principles in manufacturing
- Growing adoption of monolithic refractories
- Shift toward energy-efficient production methods
3. Market Demand Drivers
- Surge in infrastructure development projects across emerging economies
- Rising demand for specialized glass products in electronics
- Expansion of cement production facilities
- Growth in petrochemical processing capacity
4. Sustainability Initiatives
- Development of eco-friendly refractory materials
- Carbon footprint reduction in manufacturing processes
- Investment in energy-efficient kilns
- Research into alternative raw material sources
The convergence of these trends has sparked significant investments in R&D, with companies focusing on developing high-performance refractories that meet evolving industry requirements. The market’s transformation reflects broader industrial shifts toward digitalization, sustainability, and enhanced operational efficiency.
Challenges in the Refractory Materials Industry
The refractory materials industry faces significant hurdles that impact its growth and sustainability.
Environmental Regulations
Environmental regulations pose strict limitations on manufacturing processes, particularly regarding carbon emissions. Manufacturers are struggling to reduce their carbon footprint while maintaining product quality and performance.
Raw Material Sourcing
Raw material sourcing presents another critical challenge. The industry depends heavily on specific minerals and materials, many of which are:
- Subject to price volatility
- Located in geopolitically sensitive regions
- Affected by supply chain disruptions
- Limited in availability due to mining restrictions
Energy Consumption
Energy consumption remains a persistent concern. The production of refractory materials requires high-temperature processes, resulting in:
- Substantial energy costs
- Increased operational expenses
- Higher carbon emissions
- Pressure to adopt energy-efficient technologies
Skilled Labor Shortages
The industry also struggles with skilled labor shortages. Manufacturing refractories demands specialized knowledge and expertise, yet finding and retaining qualified personnel proves increasingly difficult.
Quality Control Challenges
Quality control challenges emerge as manufacturers work to meet stringent industry standards while adapting to new environmental regulations. The balance between maintaining product performance and complying with emissions standards creates additional pressure on production processes.
These challenges drive the need for innovative solutions in manufacturing processes, material sourcing, and workforce development. The industry’s response to these obstacles shapes its evolution and adaptation to changing market demands.
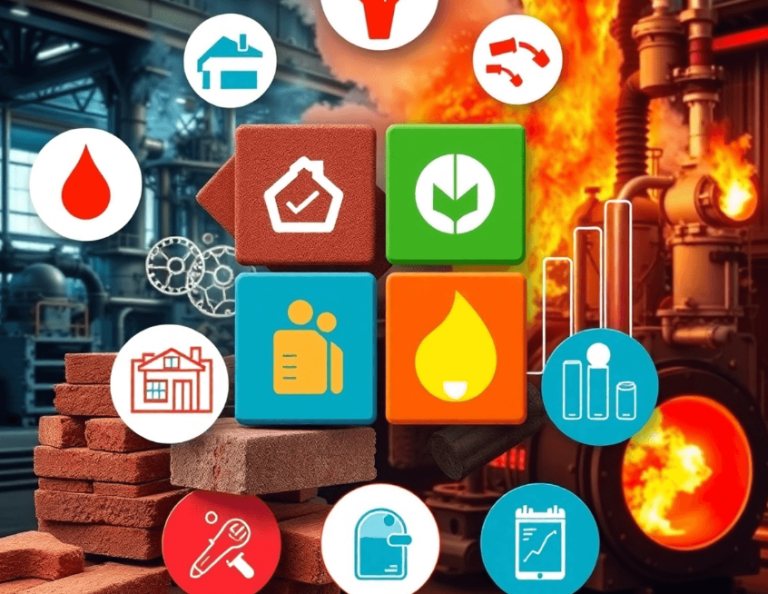
Geopolitical Influences on the Refractory Market
The refractory market’s landscape shifts dramatically with global political dynamics. Trade tensions between major economies create ripple effects throughout the supply chain, affecting both raw material availability and finished product distribution.
Key Trade Policy Impacts:
- China’s export restrictions on critical raw materials drive price volatility
- U.S. tariffs on Chinese refractory products reshape regional supply patterns
- EU’s carbon border regulations influence production costs and market access
Regional Power Dynamics:
- Russia-Ukraine conflict disrupts magnesite and alumina supply chains
- Middle East tensions affect energy costs for refractory production
- Southeast Asian manufacturing hubs emerge as alternative suppliers
The strategic importance of refractories in steel production makes them subject to national security considerations. Countries implement protective measures to safeguard domestic refractory manufacturing capabilities, leading to market fragmentation and localized production networks.
Price Implications:
- Raw material costs fluctuate with changing trade agreements
- Transportation expenses rise due to geopolitical route disruptions
- Currency exchange rates impact international trade competitiveness
Supply chain resilience becomes a priority as manufacturers diversify their sourcing strategies. Companies establish multiple production facilities across different regions to mitigate geopolitical risks and ensure consistent supply to their customers.
Types of Refractories: Fireclay, Silica, and More
Refractories come in various types, each designed for specific industrial uses. The two main categories are clay-based and non-clay refractories, each with its own characteristics and applications.
Clay-Based Refractories:
- Fireclay Refractories: Made from aluminum silicate materials, offering temperature resistance up to 1,500°C
- High Alumina: Contains 45-100% alumina, suitable for extreme temperature conditions
- Silica-Based: Composed of 93-97% silica, ideal for glass furnace crowns
Non-Clay Refractories:
- Basic Refractories: Made from magnesia or dolomite, resistant to basic slag attacks
- Special Refractories: Include zirconia and carbon-based materials for specialized applications
- Neutral Refractories: Chrome and carbon varieties for unique industrial needs
The choice of refractory type depends on:
- Operating temperature requirements
- Chemical environment exposure
- Mechanical stress tolerance
- Cost considerations
- Application-specific needs
Different industries require specific combinations of refractories. Steel manufacturing typically uses basic refractories, while glass production relies heavily on silica-based options. The cement industry often employs high-alumina varieties for their superior strength and thermal shock resistance.
Raw material quality and availability directly influence refractory performance. Advanced manufacturing techniques continue to enhance these materials’ properties, pushing the boundaries of industrial capabilities.
Applications of Refractories in Steel, Cement, and Glass Industries
Refractories in the Steel Industry
The steel industry is the largest consumer of refractory materials. They use specialized linings in blast furnaces, ladles, and converters. These critical components must withstand:
- Temperatures exceeding 1,700°C
- Aggressive chemical reactions
- Mechanical stress from molten metal
- Thermal shock during production cycles
Refractories in Cement Manufacturing
In cement manufacturing, refractories protect kiln equipment through distinct zones:
- Burning Zone: Basic brick linings resist 1,450°C temperatures
- Transition Zone: Alumina-based materials handle temperature fluctuations
- Cooling Zone: Abrasion-resistant refractories manage clinker movement
Refractories in Glass Production
Glass production has specific requirements for refractories:
- Melting Tank: Specialized chromium-zirconium materials
- Forehearth: High-alumina refractories
- Regenerator: Silica-based materials for heat recovery
Varying Performance Requirements Across Industries
The performance needs differ widely among these industries:
Steel Industry
- Slag resistance
- High thermal conductivity
- Extended service life
Cement Production
- Alkali resistance
- Thermal cycling durability
- Abrasion resistance
Glass Manufacturing
- Chemical inertness
- Precise dimensional stability
- Corrosion resistance
Each application demands specific refractory compositions tailored to operational conditions. This makes material selection crucial for achieving optimal industrial performance.
Global Refractory Market: Growth Outlook and Demand Analysis up to 2032
The global refractory market has strong growth potential, with projections indicating a market value of USD 61.76 billion by 2033. This represents a steady CAGR of 6.3% from 2024’s USD 37.88 billion valuation.
Regional Market Share
Asia-Pacific holds 65.7% market share, establishing its position as the primary growth engine for the global refractory sector. Key factors driving this regional dominance include:
- Rapid industrialization across developing economies
- Substantial investments in infrastructure development
- Growing urbanization rates
- Rising demand from emerging markets
Market Size Projections by Region through 2032
- Asia-Pacific: USD 37.64 billion
- North America: USD 8.59 billion
- Europe: USD 6.87 billion
- Rest of World: USD 4.19 billion
Demand Analysis by Application
The demand analysis reveals shifting patterns across different applications:
- Basic refractories: 42% market share
- Non-basic refractories: 35% market share
- Special refractories: 23% market share
Regional Consumption Patterns
Regional consumption patterns indicate China’s continued leadership in refractory demand, followed by India and Japan. The market forecast suggests increased demand from Southeast Asian countries, particularly Vietnam and Indonesia, driven by their expanding manufacturing sectors and infrastructure development initiatives.
The growth trajectory remains influenced by technological advancements in manufacturing processes and increasing adoption of high-performance refractory materials across industries.
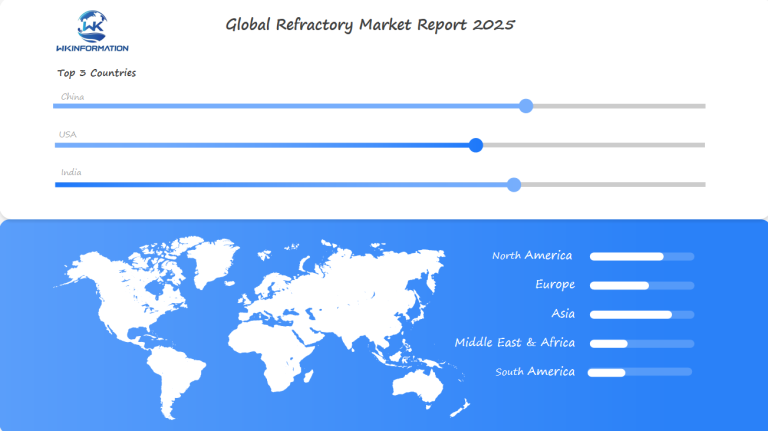
U.S. Refractory Market: Technological Innovations and Industry Trends
The U.S. refractory market is expected to reach $5.18 billion by 2032, driven by cutting-edge technological advancements and strategic R&D investments. American manufacturers are leading the way in developing smart refractory solutions with embedded sensors for real-time monitoring of wear patterns and thermal stress distribution.
Key Technological Innovations Shaping the U.S. Market
Some of the key technological innovations shaping the U.S. refractory market include:
- AI-powered predictive maintenance systems that optimize refractory lifecycle management
- Nano-engineered materials offering enhanced thermal resistance and longer service life
- 3D printing technology enabling custom-shaped refractory components
- Advanced coating technologies that improve corrosion resistance
Areas of Focus for U.S. Research and Development
U.S. companies are investing heavily in research focused on:
- Development of eco-friendly binding systems
- Integration of Internet of Things (IoT) for process optimization
- Creation of hybrid refractory materials with superior performance
The Role of the Steel Industry in Driving Innovation
The steel industry remains the primary driver of innovation, with manufacturers developing specialized refractories for electric arc furnaces and continuous casting processes. These advancements have led to a 15-20% increase in refractory life span and a significant reduction in maintenance costs.
Increased R&D Investments by U.S. Companies
R&D investments by U.S. companies have doubled since 2020, with particular emphasis on developing materials capable of withstanding temperatures exceeding 2000°C while maintaining structural integrity. This push for innovation has positioned U.S. manufacturers as global leaders in high-performance refractory solutions.
India's Refractory Market: Supply Chain Dynamics and Growth Opportunities
India’s refractory sector is at a crucial stage, fueled by rapid infrastructure development and industrial expansion. The market shows strong potential with an estimated worth of $2.5 billion by 2025.
Key Growth Drivers:
- Extensive railway infrastructure projects
- Smart city initiatives
- Expansion of steel manufacturing facilities
- Growing cement production capacity
The supply chain landscape in India’s refractory market has some distinct features:
1. Raw Material Sourcing
- 65% dependency on imported materials
- Critical minerals sourced from China and Brazil
- Rising focus on domestic mineral exploration
2. Manufacturing Hub Development
- Emergence of specialized refractory clusters
- Integration of automated production systems
- Enhanced quality control measures
Infrastructure Development Impact:
- Metro rail projects increasing demand for specialized refractories
- Power sector expansion requiring high-grade materials
- Port modernization driving specialized refractory consumption
The Indian refractory sector faces specific challenges:
- Limited availability of high-quality raw materials
- Fluctuating import costs
- Technical skill gaps in manufacturing
Growth Opportunities:
- Development of alternative raw material sources
- Investment in research facilities
- Collaboration with international technology providers
- Focus on value-added refractory products
India’s refractory market is poised for significant growth, driven by the expanding industrial sectors such as steel, cement, and glass manufacturing. As one of the largest steel producers in the world, India’s demand for refractories is closely linked to the steel industry’s performance. The country’s refractory supply chain is primarily composed of raw material suppliers, manufacturers, and distributors, with key inputs including alumina, silica, and magnesia. The supply chain is seeing increased investments in production capacities, logistics infrastructure, and technology adoption to meet the growing demand for high-performance refractories.
The establishment of dedicated freight corridors has strengthened distribution networks, enabling faster delivery and reduced logistics costs across the country.
China's Dominance in the Global Refractory Market
China is the clear leader in the global refractory market, holding a 65% market share in 2023. This dominance is primarily due to the country’s large iron and steel production capacity, which reached 1.07 billion tonnes in 2022.
Strategic Advantages of the Chinese Refractory Industry
The Chinese refractory industry has several strategic advantages:
- Raw Material Access: China controls 60% of global magnesite reserves
- Manufacturing Scale: Over 2,000 refractory production facilities
- Cost Leadership: Lower production and labor costs
- Integrated Supply Chain: Proximity to key raw materials and end-users
How the Steel Sector Drives Refractory Demand
The demand for refractories in China is primarily driven by the steel sector, which relies on various processes such as:
- Blast furnace operations
- Basic oxygen furnaces
- Electric arc furnaces
- Secondary steelmaking processes
Technological Upgrades by Chinese Manufacturers
Chinese manufacturers have made significant investments in technological upgrades, focusing on:
- Advanced automation systems
- Energy-efficient production methods
- High-performance refractory materials
Expansion of Chinese Producers through Strong Domestic Market
The strength of the domestic market has allowed Chinese producers to expand internationally, with exports reaching $2.3 billion in 2022. The main countries receiving these exports include:
- Southeast Asian nations
- Middle Eastern markets
- European Union member states
- United States
Government Initiatives Supporting Domestic Demand
The Chinese government is actively supporting infrastructure development through initiatives like the Belt and Road project, which further boosts domestic demand for refractories and solidifies China’s position as the market leader.
The Future of Refractories: Sustainable Materials, Production Practices, and Recycling Potential
The refractory industry is undergoing a significant transformation toward sustainable practices. Companies now prioritize eco-friendly production methods and recycling initiatives to reduce their environmental footprint while maintaining product quality.
Key Sustainability Initiatives:
- Implementation of energy-efficient kilns
- Development of low-carbon footprint materials
- Integration of waste heat recovery systems
- Adoption of circular economy principles
Recycled refractory materials present substantial cost-saving opportunities, with potential reductions of 15-30% in production expenses. Advanced processing techniques allow manufacturers to repurpose used refractories into new products without compromising performance.
Innovative Sustainable Materials:
- Magnesia-carbon bricks made from recycled content
- Bio-based binders replacing petroleum-derived options
- Nano-enhanced refractories requiring less raw material
- Hybrid compositions utilizing industrial by-products
The industry’s shift toward sustainability has sparked research into alternative raw materials. Scientists are developing refractories using industrial waste products, such as slag and fly ash, demonstrating promising results in thermal resistance and durability.
These sustainable practices align with global environmental regulations while meeting growing market demands. Companies investing in green technologies gain competitive advantages through reduced operational costs and enhanced brand reputation in the evolving refractory landscape.
Competitive Insights: Key Companies in the Refractory Market
The global refractory market is characterized by the dominance of several large multinational companies, each with its unique strengths in manufacturing and distribution across various industries such as steel, cement, glass, and non-ferrous metals. Among the key players are RHI Magnesita, VESUVIUS, KROSAKI, and SHINAGAWA, who are known for their innovative products and technological advancements. These companies have strong international footprints, with manufacturing facilities strategically located in key regions, allowing them to serve global markets effectively.
-
RHI Magnesita – Austria
-
VESUVIUS – Belgium
-
KROSAKI – Japan
-
SHINAGAWA – Japan
-
Imerys – France
-
HWI (HarbisonWalker International) – United States
-
Morgan Crucible – United Kingdom
-
Saint-Gobain – France
-
Minteq International Inc. – United States
-
Resco Products – United States
Overall
Report Metric | Details |
---|---|
Report Name | Global Refractory Market Report |
Base Year | 2024 |
Segment by Type |
· Clay-Based Refractories · Non-Clay Refractories |
Segment by Application |
· Steel · Cement · Glass |
Geographies Covered |
· North America (United States, Canada) · Europe (Germany, France, UK, Italy, Russia) · Asia-Pacific (China, Japan, South Korea, Taiwan) · Southeast Asia (India) · Latin America (Mexico, Brazil) |
Forecast units | USD million in value |
Report coverage | Revenue and volume forecast, company share, competitive landscape, growth factors and trends |
Refractories play a vital role across steel, cement, and glass industries, serving as the backbone of high-temperature industrial processes. Their applications are diverse and specialized, with each industry demanding specific properties and performance characteristics. In steel production, refractories enable safe containment of molten metal and resist extreme temperatures. Cement manufacturing relies on these materials to maintain kiln integrity and process efficiency.
The glass industry depends on specialized refractory solutions for furnace longevity and product quality. As industrial processes continue to evolve, the development and optimization of refractory materials remain crucial for operational efficiency, safety, and product quality across these fundamental manufacturing sectors.
Global Refractory Market Report (Can Read by Free sample) – Table of Contents
Chapter 1: Refractory Market Analysis Overview
- Competitive Forces Analysis (Porter’s Five Forces)
- Strategic Growth Assessment (Ansoff Matrix)
- Industry Value Chain Insights
- Regional Trends and Key Market Drivers
- RefractoryMarket Segmentation Overview
Chapter 2: Competitive Landscape
- Global Refractoryplayers and Regional Insights
- Key Players and Market Share Analysis
- Sales Trends of Leading Companies
- Year-on-Year Performance Insights
- Competitive Strategies and Market Positioning
- Key Differentiators and Strategic Moves
Chapter 3: Refractory Market Segmentation Analysis
- Key Data and Visual Insights
- Trends, Growth Rates, and Drivers
- Segment Dynamics and Insights
- Detailed Market Analysis by Segment
Chapter 4: Regional Market Performance
- Consumer Trends by Region
- Historical Data and Growth Forecasts
- Regional Growth Factors
- Economic, Demographic, and Technological Impacts
- Challenges and Opportunities in Key Regions
- Regional Trends and Market Shifts
- Key Cities and High-Demand Areas
Chapter 5: Refractory Emerging and Untapped Markets
- Growth Potential in Secondary Regions
- Trends, Challenges, and Opportunities
Chapter 6: Product and Application Segmentation
- Product Types and Innovation Trends
- Application-Based Market Insights
Chapter 7: Refractory Consumer Insights
- Demographics and Buying Behaviors
- Target Audience Profiles
Chapter 8: Key Findings and Recommendations
- Summary ofRefractoryMarket Insights
- Actionable Recommendations for Stakeholders
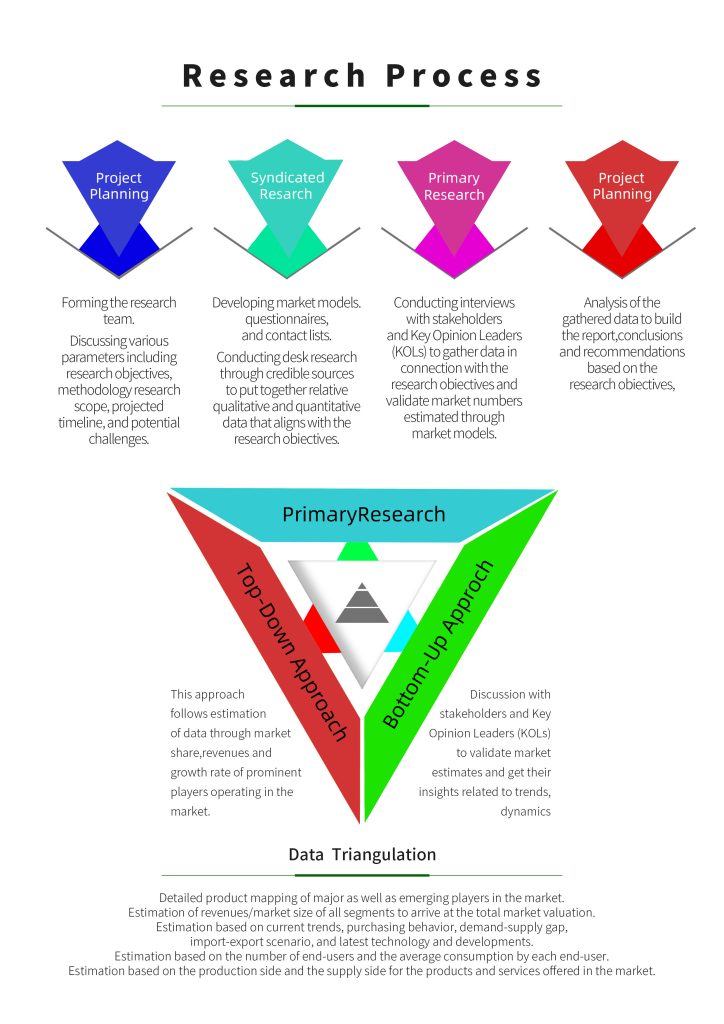
Access the study in MULTIPLEFORMATS
Didn’t find what you’re looking for?
TALK TO OUR ANALYST TEAM
Need something within your budget?
NO WORRIES! WE GOT YOU COVERED!
Call us on: +1-866-739-3133
Email: infor@wkinformation.com
What is the projected growth of the refractory market by 2025?
The refractory market in the U.S., India, and China is projected to reach $37.88 billion by 2025, reflecting significant growth driven by industrial demand.
What are the key upstream and downstream activities in the refractory industry?
Upstream activities in the refractory industry involve raw material sourcing, while downstream applications refer to how these materials are utilized in various industrial sectors, showcasing the interconnectedness of different segments within the market.
What trends are currently driving the growth of the refractory market?
Key trends include technological advancements, increased industrialization, and a rising demand from construction and manufacturing sectors, all contributing to a positive growth trajectory for the refractory market.
What challenges does the refractory materials industry face?
The refractory materials industry faces challenges such as stringent environmental regulations regarding carbon emissions and difficulties in sourcing raw materials, which can impact production and profitability.
How do geopolitical factors influence the refractory market?
Geopolitical factors such as global trade policies and regional dynamics significantly impact supply chains and pricing strategies within the refractory market, affecting overall market stability.
What types of refractories are commonly used in various industries?
Common types of refractories include fireclay and silica refractories. Each type has distinct properties suited for specific applications across industries like steelmaking, cement production, and glass manufacturing.