2025 Flux Coated Preforms Market Booming with $2.8 Billion Growth in US, China, and Germany
Explore the flux coated preforms market dynamics led by the US, China, and Germany amid trade battles and evolving industry trends.
- Last Updated:
Flux Coated Preforms Market Projection for Q1 and Q2 2025
The global flux coated preforms market, valued at USD 2.8 billion in 2025, is expected to expand at a CAGR of 6.5% from 2025 to 2033. The estimated market size in Q1 2025 is around USD 650 million, increasing to approximately USD 700 million by Q2 2025.
The US, China, and Germany dominate this market due to their well-established electronics, automotive, and aerospace industries. The US benefits from high adoption rates in soldering and brazing applications. China, as the world’s largest electronics producer, significantly drives market demand. Germany’s expertise in precision engineering and high-performance materials makes it a key player in this sector.
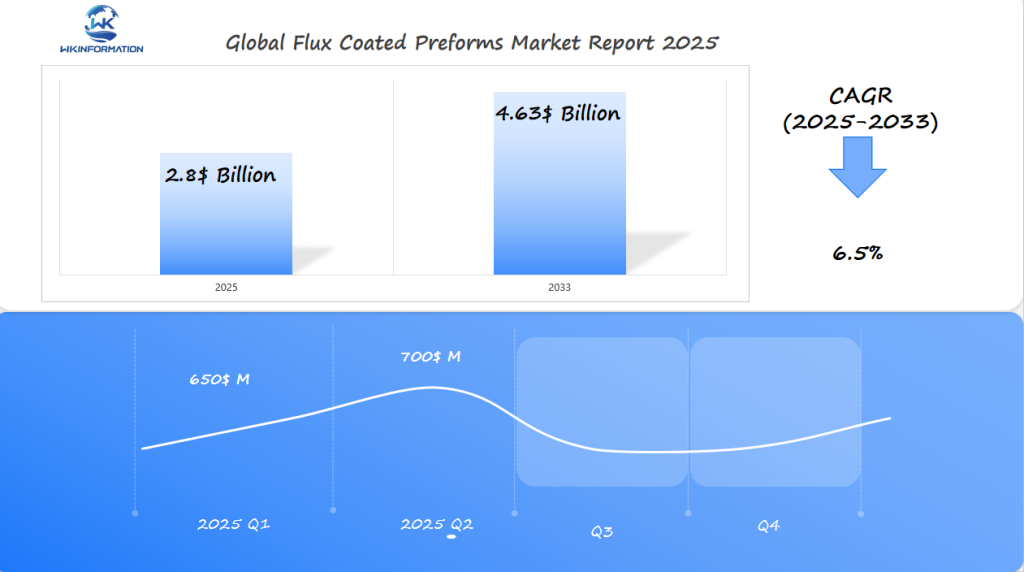
Flux Coated Preforms Market Upstream and Downstream Industry Chain Analysis
Understanding the upstream supply chain of flux coated preforms begins with raw materials. Key components include metals like tin, lead, and silver, which are essential for creating effective soldering materials. The quality of these raw materials significantly influences the performance and reliability of the final product.
Downstream demand is driven by various end-user industries that depend on flux coated preforms for critical operations. Electronics assembly stands out as a major sector, where these products ensure reliable solder joints in devices ranging from everyday gadgets to complex microelectronics. Automotive manufacturing also leans heavily on these preforms, utilizing them in electrical systems and safety components.
Advancements in manufacturing processes are reshaping market dynamics and enhancing product quality. Implementation of cutting-edge techniques such as automated precision soldering and Industry 4.0 technologies has led to improved efficiency and reduced production costs. These innovations not only boost the overall quality of flux coated preforms but also drive their adoption across diverse industries, magnifying market growth potential.
By continuously evolving both upstream and downstream aspects, the flux coated preforms market is poised for substantial development, catering to an ever-expanding range of applications.
Key Trends Driving the Flux Coated Preforms Market in 2025
1. Industry 4.0 and Smart Manufacturing
The integration of Industry 4.0 technologies is revolutionizing the flux coated preforms market by enhancing production efficiency. Smart manufacturing processes allow for real-time monitoring and automation, reducing costs and minimizing errors in production lines. These advancements result in higher quality products that meet precise industry standards.
2. Sustainability in Soldering Technologies
As industries push toward environmentally responsible practices, the adoption of sustainable soldering technologies is gaining momentum. The shift towards eco-friendly flux materials reduces harmful environmental impacts, while energy-efficient manufacturing methods contribute to lower operational costs. This trend aligns with global sustainability goals, making it a significant driver of market growth.
3. Demand for Microelectronic Devices
The surge in demand for microelectronic devices directly influences the need for specialized flux coated preforms. These preforms are vital for creating reliable solder joints necessary in advanced electronics. As technology evolves, incorporating more complex components into smaller devices, the precision and reliability offered by these preforms become ever more critical, propelling market expansion.
By focusing on these trends, the flux coated preforms industry is poised for continued growth and innovation, aligning with both technological advancements and environmental objectives.
Challenges and Market Barriers Impacting the Flux Coated Preforms Industry
Manufacturers in the flux coated preforms market face several significant challenges. The competitive landscape is marked by intense price pressures, predominantly from low-cost suppliers. This competition demands that companies maintain stringent quality control measures to ensure that their products meet industry standards without sacrificing profitability.
Regulatory challenges further complicate the market dynamics. Compliance with international regulations, particularly those concerning hazardous substances in flux formulations, poses a formidable barrier. For instance, restrictions under directives like RoHS (Restriction of Hazardous Substances) necessitate constant innovation to develop compliant materials while maintaining performance quality.
Key Challenges
- Price Pressures: Low-cost suppliers exert downward pressure on pricing strategies.
- Quality Control Requirements: Maintaining high-quality standards is crucial amidst fierce competition.
- Regulatory Challenges: Compliance with international regulations such as RoHS and development of alternative formulations to replace restricted substances.
Navigating these obstacles requires strategic planning and investment in research and development. Companies must balance cost efficiency with compliance and quality to thrive in this evolving market landscape.
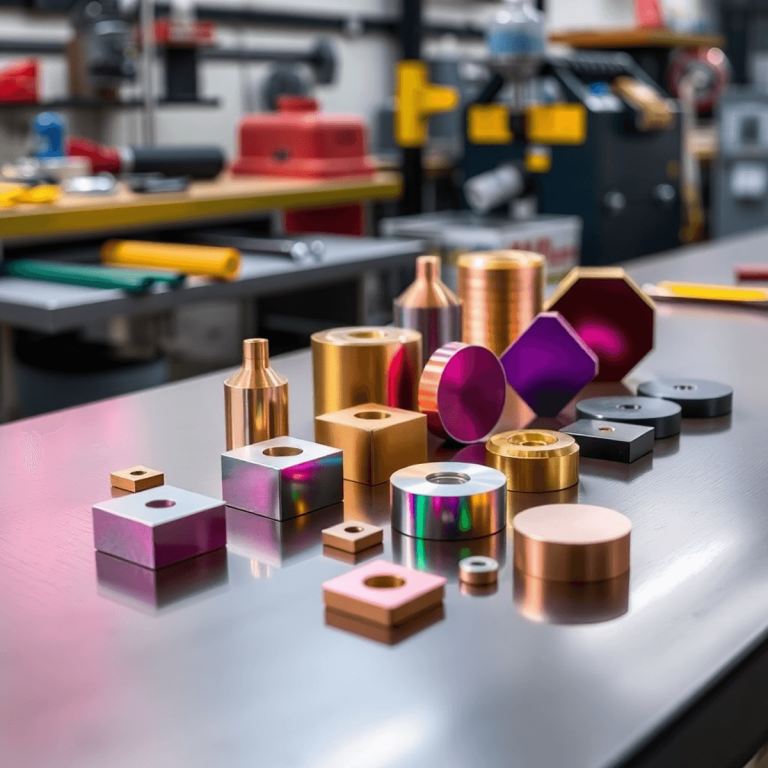
Geopolitical Influences on the Flux Coated Preforms Market Expansion
The flux coated preforms market is deeply intertwined with geopolitical factors that shape its global landscape. Trade policies implemented by various countries play a critical role in determining the import/export dynamics of these products. For instance, tariffs imposed on raw materials can directly affect production costs, influencing the pricing strategies of manufacturers. Additionally, free trade agreements or restrictions can alter the competitive landscape, impacting market accessibility for international players.
Geopolitical tensions between major economies such as the US, China, and Germany significantly impact global supply chains. These tensions can lead to uncertainties in investments, as companies may hesitate to allocate resources in regions with volatile political climates. Such instability often results in disrupted supply chains, causing delays in the delivery of essential components like flux coated preforms.
International relations further complicate these dynamics by affecting regulatory standards and compliance requirements across borders. This complexity necessitates adaptive strategies from companies to navigate potential hurdles while maintaining efficient operations. Understanding these geopolitical influences is crucial for stakeholders aiming to capitalize on growth opportunities within this expanding market segment.
Flux Coated Preforms Market Segmentation by Type and Demand Sectors
Lead-Free Flux Coated Preforms
Lead-free flux coated preforms are gaining popularity due to their environmental benefits and compliance with global regulations, such as RoHS (Restriction of Hazardous Substances). These preforms are primarily used in electronics and electrical applications where lead-free soldering is mandated. The demand for lead-free preforms is driven by the global shift toward greener manufacturing practices and the increased focus on reducing hazardous materials in production processes.
Lead-Based Flux Coated Preforms
Despite the rise of lead-free alternatives, lead-based flux coated preforms continue to be used in specific applications where their superior properties, such as better wettability and reliability in solder joints, are required. These preforms are commonly used in high-reliability sectors such as aerospace, automotive, and military applications. However, demand for lead-based preforms is gradually declining due to environmental and regulatory pressures.
No-Clean Flux Coated Preforms
No-clean flux coated preforms are used in applications where post-soldering cleaning is not required. These preforms are ideal for industries where speed and efficiency are critical, such as in high-volume electronics manufacturing. The no-clean flux leaves minimal residue, reducing the need for additional cleaning steps and enhancing the overall productivity of manufacturing processes.
Water-Soluble Flux Coated Preforms
Water-soluble flux coated preforms are designed to be cleaned easily after soldering using water, making them suitable for applications where clean soldering joints are essential. These preforms are commonly used in the automotive and medical device industries, where cleanliness and high-quality soldering joints are required for safety and performance.
Application Scope of Flux Coated Preforms and Market Growth Potential
Flux coated preforms have a wide range of applications in various industries, which greatly contributes to their potential for market growth.
1. Electronics Assembly
In the world of electronics assembly, flux coated preforms are essential for creating reliable solder joints in complex microelectronic devices. As electronic components become more intricate and miniaturized, the demand for high-performance flux coated preforms also increases.
2. Automotive Manufacturing
In the automotive manufacturing industry, flux coated preforms are crucial for ensuring strong and long-lasting connections within electrical systems. With the automotive industry moving towards more advanced and interconnected vehicles, the need for efficient soldering solutions becomes even more important.
3. Renewable Energy Systems
Emerging sectors like renewable energy systems offer promising opportunities for growth. Solar panels and wind turbines require precise and dependable soldering techniques to improve their performance and lifespan, leading to an increased use of flux coated preforms in these applications.
4. Aerospace Engineering
Another growing field is aerospace engineering, where there is a demand for lightweight yet sturdy materials. This drives the need for innovative soldering solutions, such as flux coated preforms, to meet the requirements of this industry.
These applications demonstrate the wide range of industries that utilize flux coated preforms. They highlight the significance of these components in driving market expansion as industries continue to evolve.
Global Flux Coated Preforms Market Regional Analysis and Future Demand
North America
The North American flux coated preforms market is expected to see steady growth due to the presence of a robust electronics and automotive manufacturing sector. The United States, in particular, is a key player in the market, driven by the demand for advanced soldering solutions in high-tech industries such as aerospace, automotive, and consumer electronics. Additionally, the adoption of stricter environmental regulations, such as RoHS compliance, is pushing the demand for lead-free and environmentally friendly soldering solutions.
Future Demand: The future demand in North America will likely be driven by continued technological advancements in electronics, aerospace, and automotive sectors, along with the ongoing shift toward sustainable manufacturing practices.
Europe
Europe is a significant market for flux coated preforms, driven by stringent regulations concerning environmental sustainability and product safety, particularly in industries like electronics, automotive, and aerospace. Countries such as Germany, France, and the UK are key players in this region, where flux coated preforms are widely used in automotive manufacturing, especially with the rise of electric vehicles (EVs) and automation.
Future Demand: The demand in Europe is expected to increase, especially with the EU’s focus on sustainability and the growing use of flux coated preforms in EVs and next-generation electronic devices.
Asia-Pacific
The Asia-Pacific region holds the largest market share for flux coated preforms, primarily due to the region’s dominance in electronics manufacturing, automotive production, and consumer goods. China, Japan, South Korea, and India are key contributors to the market, where flux coated preforms are widely used in electronics and automotive applications.
Future Demand: The Asia-Pacific region is expected to continue to lead the market, with demand driven by the ongoing industrial growth, technological advancements, and increased adoption of sustainable and environmentally friendly flux coated preforms.
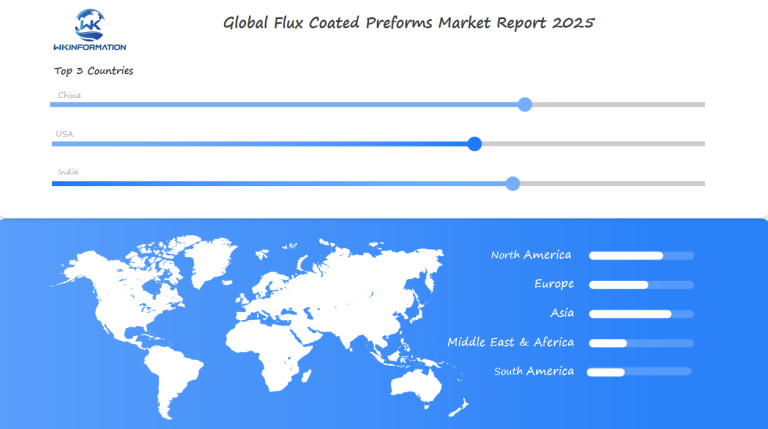
US Flux Coated Preforms Market Growth and Competitive Insights
The U.S. flux-coated preforms market is expected to experience steady growth in the coming years due to advancements in manufacturing technologies, increasing demand for high-precision soldering in various sectors, and the need for environmentally friendly solutions. The market is driven by the growing industries of electronics, automotive, aerospace, and medical devices, where flux-coated preforms play a critical role in ensuring high-quality soldering and bond formation.
Growth Drivers for the U.S. Flux-Coated Preforms Market
Expansion of the Electronics and Semiconductor Industry
-
The electronics sector is one of the largest drivers of flux-coated preform demand. With the continued growth in consumer electronics (smartphones, wearables, etc.), semiconductor packaging, PCBs, and electronic assembly are major applications of flux-coated preforms. The need for high-reliability soldering in these sensitive components is boosting demand for flux-coated preforms.
-
5G deployment and Internet of Things (IoT) technologies also increase the need for high-precision electronics and soldering techniques, further stimulating the demand for flux-coated preforms.
Shift Toward Electric Vehicles (EVs)
-
-
The rise of electric vehicles in the automotive sector is a significant growth driver. Electric vehicles require advanced soldering for various electronic components, including battery management systems (BMS), connectors, and power electronics. Flux-coated preforms are used extensively in these applications to ensure the performance and reliability of the vehicle’s electronic components.
-
The U.S. government’s push for green energy and EV adoption, combined with incentives for EV manufacturers, is fueling the demand for flux-coated preforms in the automotive sector.
-
Aerospace and Defense Industry Requirements
-
-
The aerospace and defense sectors require high-reliability soldering for components in satellites, aircraft, and military electronics. Flux-coated preforms are essential in soldering components that must meet stringent safety and performance standards.
-
The ongoing military modernization efforts and growing investment in space exploration contribute to the increasing use of flux-coated preforms in critical applications.
-
Germany Flux Coated Preforms Market Expansion and Investment Trends
The Germany flux-coated preforms market is expected to expand significantly over the next few years, driven by several factors, including advancements in electronics manufacturing, the rise of electric vehicles (EVs), and increasing demand from the aerospace and medical device sectors. As a key player in the European manufacturing landscape, Germany’s demand for flux-coated preforms is supported by its strong industrial base, regulatory frameworks, and investments in sustainable manufacturing technologies.
Key Factors Driving Market Expansion in Germany
Strong Electronics and Semiconductor Manufacturing Hub
-
-
Germany is a global leader in the electronics and semiconductor manufacturing sectors, making it a key driver of the flux-coated preforms market. The demand for flux-coated preforms in this sector is primarily fueled by the need for precision soldering in printed circuit boards (PCBs), semiconductor packaging, and other electronic components.
-
The growth of 5G networks, IoT devices, and smart consumer electronics is pushing for increasingly sophisticated soldering technologies, creating demand for flux-coated preforms that offer superior soldering properties and reliability.
-
Expansion of Electric Vehicle (EV) Manufacturing
-
-
The automotive industry in Germany is undergoing a significant transformation, with a strong shift toward electric vehicles (EVs). Germany’s automotive giants, including Volkswagen, BMW, and Mercedes-Benz, are heavily investing in electric vehicle production, requiring flux-coated preforms for battery management systems (BMS), power electronics, charging systems, and other high-performance components.
-
As part of Germany’s green transition, the demand for environmentally friendly, lead-free flux-coated preforms is increasing, especially in the context of sustainable manufacturing and regulatory requirements like RoHS (Restriction of Hazardous Substances).
-
China Flux Coated Preforms Market Performance and Market Forecast
The China flux-coated preforms market is expected to experience strong growth over the next few years, driven by the country’s position as a global manufacturing hub, the rise of key industries such as electronics, automotive, and aerospace, and increasing demand for high-performance soldering solutions. China’s continuous investment in innovation, along with the government’s focus on upgrading industries and improving product quality, is fueling the growth of the flux-coated preforms market.
Key Factors Driving the China Flux-Coated Preforms Market
Growth of the Electronics and Semiconductor Industries
-
-
China is one of the largest producers and consumers of electronics and semiconductors in the world. The demand for flux-coated preforms in this sector is driven by the growing need for printed circuit boards (PCBs), semiconductor packaging, LED lighting, and other electronic components. The increase in demand for smart devices, 5G technology, IoT devices, and consumer electronics is a key factor propelling the need for flux-coated preforms in electronics manufacturing.
-
As the country continues to build and modernize its semiconductor production facilities, the demand for high-quality soldering materials will continue to rise. Flux-coated preforms play a crucial role in providing the reliability and precision required for these components.
-
Rapid Expansion of the Electric Vehicle (EV) Market
-
-
China is the largest market for electric vehicles (EVs) globally, and this expansion is a significant driver for flux-coated preforms. Electric vehicle manufacturers require high-quality soldering materials for components such as battery management systems (BMS), power electronics, and charging systems. The growing production of EVs, combined with government incentives for EV manufacturers, further fuels the demand for flux-coated preforms in the automotive sector.
-
Flux-coated preforms are crucial for soldering in high-precision applications like battery connectors, motors, and powertrain systems in electric vehicles, which must meet stringent reliability and performance standards.
-
Future Innovations and Technology Advancements Shaping the Flux Coated Preforms Market Landscape
Technology advancements and innovation trends are crucial in shaping the future of the flux coated preforms market. Research is leading the way in developing new soldering materials that offer better performance.
Key Innovations
Some of the key innovations in this field include:
- Higher Thermal Fatigue Resistance: New soldering materials are being designed to withstand extreme temperature changes, which is essential for applications in electronics and automotive industries.
- Improved Conductivity and Strength: Efforts are being made to enhance the conductivity and mechanical strength of flux coated preforms. This ensures reliability and durability in demanding environments.
- Eco-Friendly Compositions: Researchers are looking into sustainable alternatives to traditional materials, aiming to reduce environmental impact without compromising quality or performance.
- Nanotechnology Integration: The use of nanomaterials shows promise in improving the properties of flux coatings, thereby increasing their effectiveness in microelectronic applications.
Continuous innovation not only solves current problems but also opens up opportunities for new applications in various industries. These advancements play a significant role in maintaining a competitive edge in this ever-changing market.
Competitive Landscape and Leading Players in the Flux Coated Preforms Market
In the competitive landscape of the Flux Coated Preforms Market, several key players stand out due to their significant market share and innovative product offerings. Among these, Indium Corporation holds a prominent position. With an extensive product portfolio that caters to diverse applications, Indium Corporation’s dominance is attributed to its commitment to quality and technological advancements.
-
Ametek – United States
-
Alpha – United States
-
Kester – United States
-
Indium Corporation – United States
-
Pfarr – Germany
-
Nihon Handa – Japan
-
SMIC (Semiconductor Manufacturing International Corporation) – China
-
Harris Products – United States
-
AIM Solder – United States
-
Nihon Superior – Japan
Overall
Report Metric | Details |
---|---|
Report Name | Global Flux Coated Preforms Market Report |
Base Year | 2024 |
Segment by Type |
· Lead-Free Flux Coated Preforms · Lead-Based Flux Coated Preforms · No-Clean Flux Coated Preforms · Water-Soluble Flux Coated Preforms |
Segment by Application |
· Electronics Assembly · Automotive Manufacturing · Renewable Energy Systems · Aerospace Engineering |
Geographies Covered |
· North America (United States, Canada) · Europe (Germany, France, UK, Italy, Russia) · Asia-Pacific (China, Japan, South Korea, Taiwan) · Southeast Asia (India) · Latin America (Mexico, Brazil) |
Forecast units | USD million in value |
Report coverage | Revenue and volume forecast, company share, competitive landscape, growth factors and trends |
Flux Coated Preforms Market analysis shows a huge growth potential and is expected to increase to $2.8 billion by 2025. This growth is primarily driven by technological advancements, growing demand from various industries, and a strong market presence in key regions such as the U.S., Germany, and China.
Global Flux Coated Preforms Market Report (Can Read by Free sample) – Table of Contents
Chapter 1: Flux Coated Preforms Market Analysis Overview
- Competitive Forces Analysis (Porter’s Five Forces)
- Strategic Growth Assessment (Ansoff Matrix)
- Industry Value Chain Insights
- Regional Trends and Key Market Drivers
- Flux Coated PreformsMarket Segmentation Overview
Chapter 2: Competitive Landscape
- Global Flux Coated PreformsPlayers and Regional Insights
- Key Players and Market Share Analysis
- Sales Trends of Leading Companies
- Year-on-Year Performance Insights
- Competitive Strategies and Market Positioning
- Key Differentiators and Strategic Moves
Chapter 3: Flux Coated Preforms Market Segmentation Analysis
- Key Data and Visual Insights
- Trends, Growth Rates, and Drivers
- Segment Dynamics and Insights
- Detailed Market Analysis by Segment
Chapter 4: Regional Market Performance
- Consumer Trends by Region
- Historical Data and Growth Forecasts
- Regional Growth Factors
- Economic, Demographic, and Technological Impacts
- Challenges and Opportunities in Key Regions
- Regional Trends and Market Shifts
- Key Cities and High-Demand Areas
Chapter 5: Flux Coated Preforms Emerging and Untapped Markets
- Growth Potential in Secondary Regions
- Trends, Challenges, and Opportunities
Chapter 6: Product and Application Segmentation
- Product Types and Innovation Trends
- Application-Based Market Insights
Chapter 7: Flux Coated Preforms Consumer Insights
- Demographics and Buying Behaviors
- TargetAudience Profiles
Chapter 8: Key Findings and Recommendations
- Summary of Flux Coated Preforms Market Insights
- Actionable Recommendations for Stakeholders
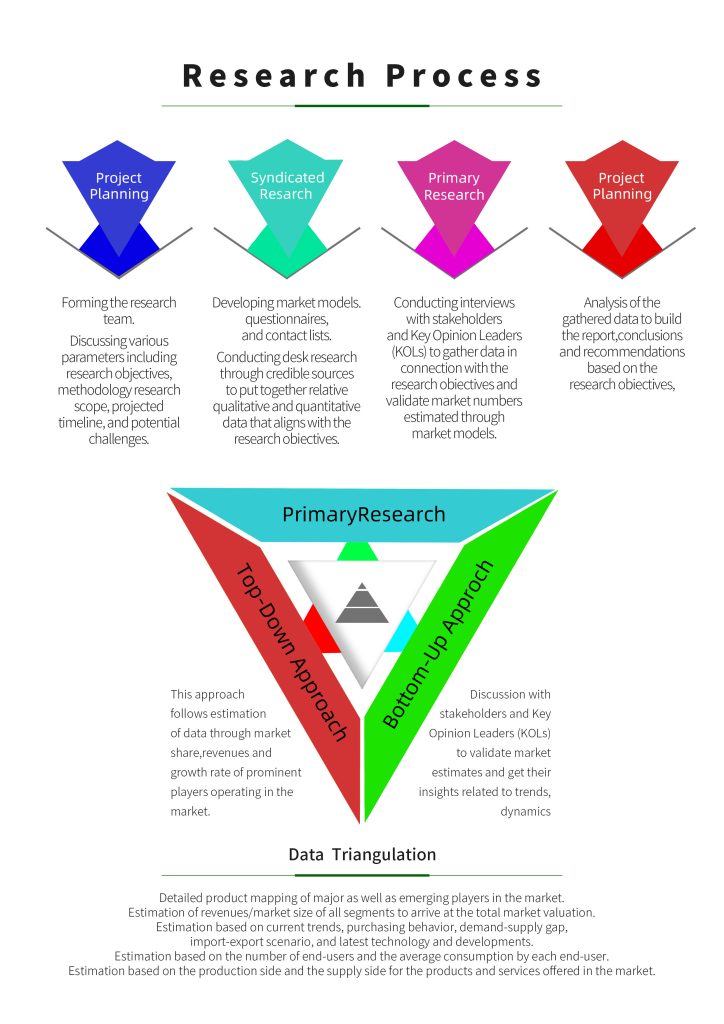
Access the study in MULTIPLEFORMATS
Didn’t find what you’re looking for?
TALK TO OUR ANALYST TEAM
Need something within your budget?
NO WORRIES! WE GOT YOU COVERED!
Call us on: +1-866-739-3133
Email: infor@wkinformation.com
What is the projected growth of the flux coated preforms market by 2025?
The flux coated preforms market is projected to experience substantial growth, with an anticipated increase of $2.8 billion by 2025, primarily driven by key regions such as the US, China, and Germany.
What are the key industries that utilize flux coated preforms?
Flux coated preforms are extensively used in various industries including electronics assembly, automotive manufacturing, and emerging sectors like renewable energy systems and aerospace engineering.
What challenges does the flux coated preforms industry face?
Manufacturers in the flux coated preforms industry face major challenges such as price pressures from low-cost suppliers, stringent quality control requirements, and regulatory compliance issues related to hazardous substances in flux formulations.
How do geopolitical factors influence the flux coated preforms market?
Geopolitical factors, including trade policies and international relations, significantly affect the import/export dynamics of flux coated preforms and can disrupt global supply chains and investments in this sector.
What technological advancements are shaping the future of the flux coated preforms market?
Ongoing research efforts are focused on developing novel soldering materials with improved performance characteristics, such as higher thermal fatigue resistance, which are expected to shape the future landscape of the flux coated preforms market.
Which regions are considered key players in driving growth within the flux coated preforms market?
The US, Germany, and China are key players driving growth in their respective markets due to factors such as a robust electronics industry in the US, a thriving automotive sector in Germany, and rapid industrialization experienced by China.