Anti-Corrosion Pigment Market Insights: $37.9 Billion Global Growth by 2025 with Key Insights from the U.S., China, and Brazil
Explore the evolving landscape of anti-corrosion pigments market, from infrastructure demands to technological innovations. Discover key trends, regional opportunities, and market dynamics shaping this essential industrial sector, with insights into sustainable solutions and strategic growth initiatives across global markets.
- Last Updated:
Anti-corrosion Pigment Market Q1 and Q2 2025 Forecast
The Anti-corrosion Pigment market is a key segment within the larger anti-corrosion coating industry, which is projected to reach $37.9 billion in 2025, growing at a CAGR of 3.6% from 2025 to 2033. In Q1 2025, the market is expected to generate approximately $9.5 billion, driven by the growing need for protective coatings in industrial applications, marine environments, and automotive industries.
In Q2 2025, the market is expected to reach $9.7 billion, with demand boosted by industrial expansion in key countries such as the U.S., China, and Brazil. The U.S. will remain a dominant player in anti-corrosion coatings due to stringent environmental regulations and an increasing focus on long-lasting materials in infrastructure and construction.
The use of anti-corrosion pigments will continue to grow in line with the increased demand for durable coatings that protect against harsh environmental conditions, particularly in sectors like oil & gas, marine transportation, and energy generation.
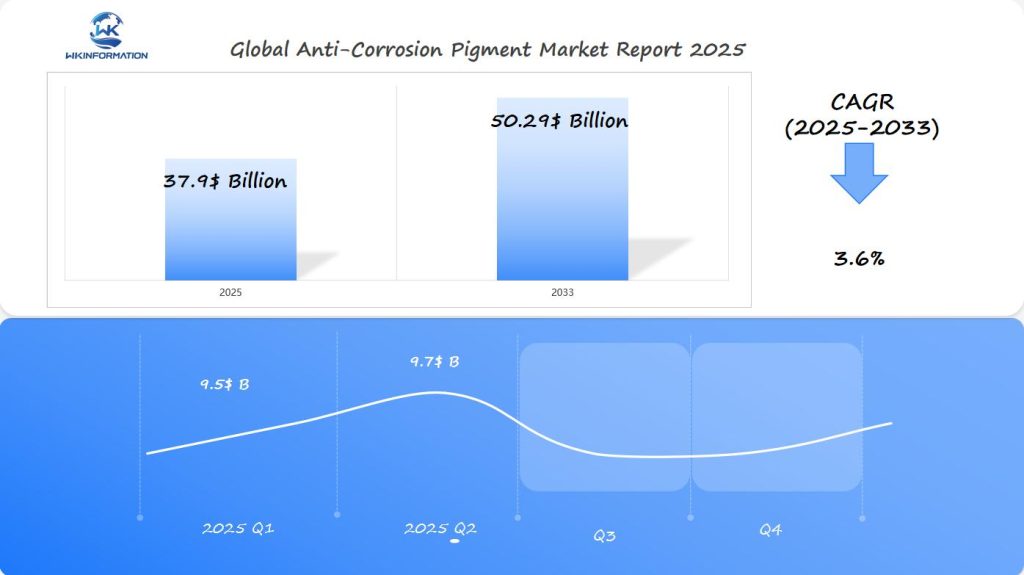
Upstream and Downstream Dynamics of Anti-Corrosion Pigment Production
The anti-corrosion pigment supply chain involves a network of various players, including raw material suppliers, manufacturers, distributors, and end-users. Let’s break down the key components of this supply chain:
1. Upstream Dynamics: Raw Material Sourcing and Manufacturing
The production of anti-corrosion pigments starts with the extraction and processing of essential raw materials. These materials are crucial for the manufacturing process and include:
- Zinc dust and zinc oxide
- Chromates and phosphates
- Metal oxides (iron, aluminum)
- Specialty chemicals and binders
- Organic compounds
Once the raw materials are sourced, they undergo various manufacturing processes to transform them into pigments. The key steps in this process include:
- Grinding and dispersion of pigments
- Chemical precipitation
- Surface treatment
- Quality control testing
- Packaging and distribution
To ensure efficient production, specialized equipment is used for tasks such as particle size reduction, surface modification, and stabilization. Modern facilities also employ automated systems to maintain precise control over critical parameters like temperature, pressure, mixing ratios, and reaction conditions.
2. Downstream Dynamics: Formulation and Distribution
After the pigments are manufactured, they need to be formulated into ready-to-use coating systems. This involves combining the pigments with other ingredients such as resins, solvents, and additives to create a paint or coating product.
Once the formulation is complete, the coatings are packaged for distribution. This can involve different types of packaging depending on the end-user requirements – such as drums for industrial applications or smaller containers for retail.
The final step in the downstream operations is distributing the finished products to industrial users or retailers. Efficient logistics management plays a crucial role in ensuring timely delivery and minimizing transportation costs.
3. Challenges in the Supply Chain
The anti-corrosion pigment supply chain faces several challenges that can impact its efficiency and profitability:
- Raw material price volatility: Fluctuations in prices of key raw materials can affect production costs and profit margins.
- Transportation costs: Rising fuel prices or logistical disruptions can increase transportation expenses, impacting overall competitiveness.
To mitigate these challenges, manufacturers are adopting vertical integration strategies where they seek to control critical components of their supply chain by acquiring or establishing partnerships with suppliers or distributors.
4. Technological Advancements for Sustainability
In recent years, there have been significant advancements in production methods that aim to improve efficiency while reducing waste generation:
- Implementation of lean manufacturing principles to optimize resource utilization
- Adoption of green chemistry practices to minimize hazardous substances used in formulations
- Investment in renewable energy sources for powering manufacturing facilities
These initiatives not only contribute towards sustainability goals but also align with growing consumer demand for environmentally friendly products.
Key Trends and Technological Developments in Anti-Corrosion Pigments
The anti-corrosion pigment industry has embraced eco-friendly innovations that reshape protective coating solutions. Water-based coating systems now lead the market, offering reduced VOC emissions while maintaining high performance standards. These systems integrate naturally-derived materials and bio-based alternatives, creating sustainable protection without compromising effectiveness.
Smart coating technologies represent a significant breakthrough in the sector. These advanced solutions incorporate:
- Self-healing properties that automatically repair minor damage
- Color-changing indicators that signal corrosion onset
- Nano-engineered particles for enhanced barrier protection
Research developments have produced hybrid coating systems that combine multiple protective mechanisms:
- Barrier protection through advanced polymer technology
- Active corrosion inhibition using intelligent release systems
- Galvanic protection with zinc-rich formulations
The push toward sustainability has sparked innovation in green pigment alternatives. Manufacturers now utilize:
- Calcium phosphate-based inhibitors
- Modified graphene oxide
- Plant-derived tannins
These sustainable options deliver comparable or superior protection to traditional chromate-based pigments while meeting strict environmental regulations. The integration of artificial intelligence in formulation development speeds up the creation of new, effective anti-corrosion solutions, enabling rapid testing and optimization of coating performance.
Recent advancements in surface preparation technologies enhance coating adhesion and longevity. Plasma treatment and nano-roughening techniques create optimal surfaces for coating application, improving the overall effectiveness of anti-corrosion systems.
Understanding the Challenges Facing the Anti-Corrosion Pigment Market
The anti-corrosion pigment industry faces significant regulatory hurdles that shape product development and market access. The International Maritime Organization (IMO) has implemented strict regulations on volatile organic compounds (VOC) emissions, pushing manufacturers to reformulate their products. These regulations require extensive testing and certification processes, adding substantial costs to production.
Environmental Compliance Challenges:
- Strict limits on heavy metal content in pigments
- Requirements for reduced VOC emissions
- Mandatory environmental impact assessments
- Complex waste disposal regulations
The drive for eco-friendly solutions has created a paradox: manufacturers must maintain high performance standards while reducing environmental impact. This balance often requires substantial investment in research and development, impacting profit margins.
Market Entry Barriers:
- High initial capital requirements
- Complex technical expertise needs
- Established patent landscapes
- Stringent quality control standards
The competitive landscape presents additional challenges for both existing players and new entrants. Large manufacturers dominate market share through established distribution networks and long-term customer relationships. Smaller companies struggle to compete due to limited resources for research and development.
Raw material price volatility adds another layer of complexity to the market. Manufacturers must carefully manage their supply chains while maintaining competitive pricing strategies. This challenge is particularly acute for specialty pigment producers who rely on specific raw materials.
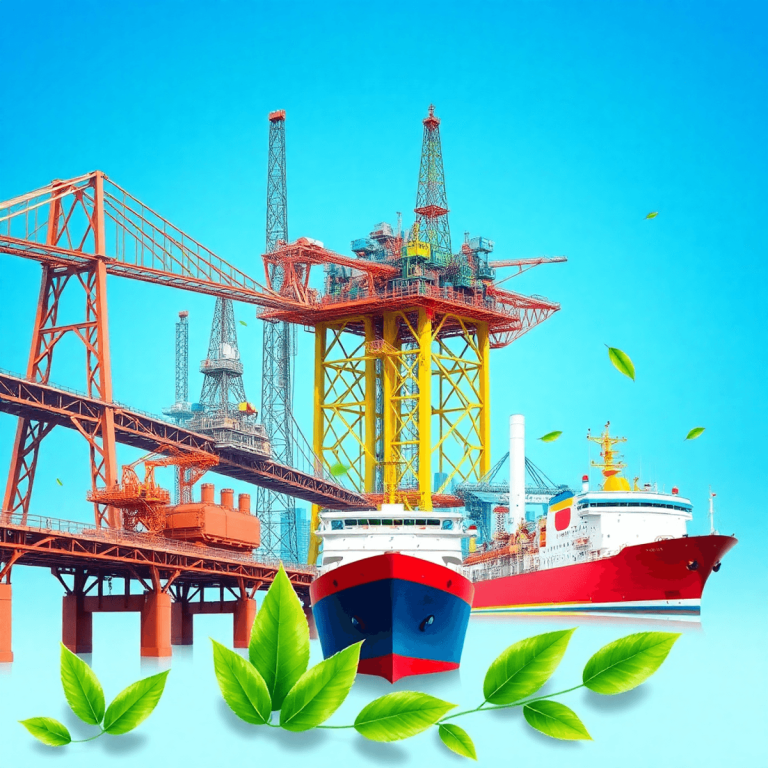
Geopolitical Factors Impacting Anti-Corrosion Pigment Trade
The anti-corrosion pigment market is currently facing significant disruptions due to changing global trade dynamics. Recent trade policies between major economies have created a complex web of challenges for manufacturers and suppliers.
1. Trade Policy Impact:
- Shifting diplomatic relations reshape supply routes
- Regional trade agreements influence market access
- Export restrictions affect raw material availability
The implementation of new tariffs has triggered price volatility across the supply chain. U.S.-China trade tensions have resulted in:
- 25% increase in raw material costs
- Supply chain diversification efforts
- Emergence of alternative manufacturing hubs in Southeast Asia
2. Market Accessibility Changes:
- Import duties affecting product competitiveness
- Varying regulatory standards between regions
- Currency fluctuations impacting pricing strategies
Recent geopolitical developments have forced industry players to adapt their strategies. Companies now focus on:
- Building regional manufacturing capabilities
- Developing local supplier networks
- Creating stockpiles to buffer against trade disruptions
The Russia-Ukraine conflict has particularly affected titanium dioxide supplies, a crucial component in anti-corrosion pigments. This has led to:
- Price spikes in European markets
- Increased demand for alternative materials
- Strategic partnerships with new suppliers
These market dynamics have pushed manufacturers to explore domestic production capabilities and invest in research for alternative materials, reshaping the industry’s competitive landscape.
Market Segmentation: Different Types of Anti-Corrosion Pigments
The anti-corrosion pigment market features distinct product categories, each serving specific industrial needs:
1. Epoxy Coatings
- Superior adhesion to metal surfaces
- High chemical resistance
- Ideal for marine environments
- Temperature resistance up to 250°F
- Used in oil refineries, chemical plants
2. Polyurethane Coatings
- Excellent UV resistance
- High gloss retention
- Flexible coating properties
- Impact and abrasion resistant
- Popular in automotive applications
3. Zinc-based Coatings
- Sacrificial protection mechanism
- Self-healing properties
- Extended service life
- Effective in harsh environments
- Common in bridge construction
4. Solvent-borne vs. Waterborne Technologies
Solvent-borne Coatings
- Fast drying time
- Better adhesion properties
- Higher VOC content
- Traditional market dominance
Waterborne Coatings
- Environmentally friendly
- Lower VOC emissions
- Easier cleanup
- Growing market share
- Reduced fire hazards
The market shows increasing preference for waterborne technologies, driven by stricter environmental regulations and workplace safety requirements. These eco-friendly alternatives deliver comparable performance while meeting sustainability goals.
Application Analysis: Where Anti-Corrosion Pigments Are in Demand
Anti-corrosion pigments are essential in various industries, each with its own specific challenges and needs for protective coatings.
Marine Sector Applications
In the marine sector, anti-corrosion pigments are used in the following ways:
- Ship hulls face constant exposure to saltwater corrosion
- Offshore platforms require specialized zinc-rich primers
- Port infrastructure demands high-performance coating systems
- Naval vessels utilize advanced multi-layer protection schemes
Infrastructure Projects
For infrastructure projects, such as bridges and highways, anti-corrosion pigments play a crucial role in:
- Bridge supports benefiting from epoxy-based protective systems
- Highway guardrails employing zinc phosphate pigments
- Underground pipelines using specialized barrier coatings
- Steel-reinforced concrete structures requiring penetrating inhibitors
Industrial Applications
In industrial settings, including chemical processing and power generation facilities, anti-corrosion pigments are applied as follows:
- Chemical processing plants utilizing acid-resistant coatings
- Power generation facilities deploying high-temperature solutions
- Storage tanks implementing sacrificial protection systems
- Manufacturing equipment requiring wear-resistant barriers
Case Study: Sydney Harbour Bridge
The iconic structure demonstrates the effectiveness of anti-corrosion pigments in extreme conditions. The bridge’s maintenance program includes zinc-rich primers and high-build epoxy intermediate coats, protecting 485,000 square meters of steel. This system has reduced maintenance costs by 40% while extending the coating lifecycle to 20+ years.
Case Study: Gulf of Mexico Oil Platforms
Offshore platforms utilize specialized three-coat systems incorporating zinc-rich primers, epoxy intermediates, and polyurethane topcoats. These systems have demonstrated 15+ years of protection in severe marine environments, reducing maintenance intervals by 60%.
Regional Growth Opportunities in the Anti-Corrosion Pigment Market
U.S. Infrastructure Investment Landscape
The U.S. infrastructure investment landscape presents significant growth opportunities for the anti-corrosion pigment market. The Infrastructure Investment and Jobs Act allocates $550 billion in new federal investments across roads, bridges, and major projects through 2026, creating substantial demand for protective coatings.
Key Growth Drivers in the U.S. Market
Aging Infrastructure Rehabilitation
- 42% of bridges are over 50 years old
- 231,000 bridges require repair or preservation work
- $125 billion estimated spending on bridge maintenance
Government-Backed Initiatives
- Build Back Better program
- Clean Energy initiatives
- Maritime infrastructure development
The U.S. Department of Transportation’s focus on extending infrastructure lifespan has sparked increased adoption of advanced anti-corrosion solutions. Recent projects showcase this trend:
“The Gateway Program’s Hudson Tunnel Project incorporates next-generation protective coatings, representing a $16 billion investment in infrastructure longevity” – American Coatings Association
Regional Demand Drivers Beyond Traditional Infrastructure
Regional market growth extends beyond traditional infrastructure, with renewable energy installations driving demand for specialized anti-corrosion pigments. Wind turbine installations alone require protective coatings for 8,000+ components per turbine.
Private sector investments complement public spending, with chemical plants and manufacturing facilities upgrading their corrosion protection systems to meet stricter environmental standards and safety requirements.
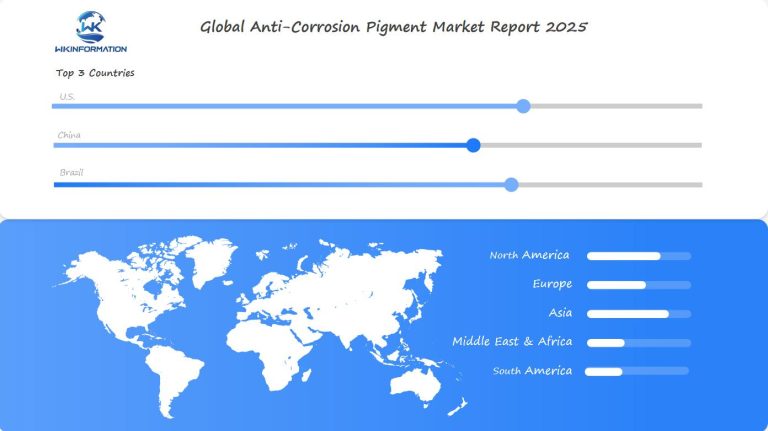
U.S. Anti-Corrosion Pigment Market: Drivers and Trends
The U.S. anti-corrosion pigment market is experiencing strong growth due to specific industry demands and regulatory requirements. Here are the key factors driving this market:
1. Industrial Sector Demands
Several industries are driving the demand for anti-corrosion pigments:
- Oil and gas exploration activities are expanding rapidly
- The automotive manufacturing sector is growing
- The aerospace industry has increasing requirements
- Power generation facilities have rising demand
2. Regulatory Influences
Regulations also play a significant role in shaping the market:
- The EPA promotes low-VOC coating solutions through its regulations
- NACE International sets standards for corrosion prevention
- ASTM specifies requirements for protective coating systems
The U.S. market has specific preferences when it comes to anti-corrosion technologies:
- Smart Coatings: These coatings have self-healing properties and can be monitored in real-time
- Nano-engineered Solutions: Graphene-based protective coatings are being developed using nanotechnology
- Bio-based Alternatives: There is a growing adoption of environmentally sustainable options
Recent data shows that there is a shift towards water-based systems in the market. U.S. manufacturers are investing heavily in research and development to come up with innovative solutions. The defense sector, particularly naval applications requiring specialized anti-corrosion treatments, remains a significant consumer of these products.
Price Sensitivity Analysis
Several factors related to pricing also impact the market:
- Raw material costs influence how products are developed
- Energy prices affect manufacturing processes
- Labor costs play a role in production decisions
The U.S. market continues to be a leader in technology, with domestic companies focusing on creating high-performance specialty coatings for critical applications.
China’s Impact on Global Anti-Corrosion Pigment Production
China is the world’s largest manufacturer of anti-corrosion pigments, controlling approximately 40% of global production capacity. The country’s manufacturing success can be attributed to several factors:
1. Advanced Production Infrastructure
China has invested heavily in its production infrastructure, which includes:
- 150+ dedicated manufacturing facilities
- Automated production lines
- State-of-the-art quality control systems
2. Strategic Export Networks
Chinese manufacturers have developed sophisticated export networks, allowing them to ship anti-corrosion pigments to over 120 countries. This strategic approach has contributed to the country’s significant export volume, which reached $12.3 billion in 2023—a 15% increase from the previous year.
3. Understanding Domestic Market Dynamics
In addition to exports, China also has a strong domestic market for anti-corrosion pigments. The dynamics of this market are as follows:
- Local consumption accounts for 60% of production
- The export market represents 40% of production
- Domestic demand has been growing at a rate of 8.5% year-over-year
Strategic Production Approaches in China’s Anti-Corrosion Pigment Sector
The Chinese anti-corrosion pigment sector embraces strategic production approaches to maintain its competitive edge:
1. Raw Material Integration
Chinese manufacturers have established direct partnerships with mineral suppliers and implemented vertical integration of supply chains. This allows them to have better control over their raw materials and reduce production costs.
2. Innovation Focus
Investments in research and development (R&D) are crucial for staying ahead in the industry. Chinese manufacturers are focusing on developing new technologies such as nano-pigment technology, water-based alternatives, and smart coating solutions.
Adapting Production Strategies to Meet Market Demands
To meet the evolving demands of the market, Chinese manufacturers are adapting their production strategies:
- Increasing automation in manufacturing processes
- Enhancing quality standards to meet international requirements
- Implementing environmental compliance measures
- Optimizing supply chains for efficiency
Expanding Production Capabilities
China’s production capabilities continue to expand with new facilities being constructed in industrial hubs like Guangdong and Jiangsu provinces. These developments further strengthen China’s position in the global anti-corrosion pigment market and ensure its ability to meet increasing demand both domestically and internationally.
Brazil’s Growing Role in the Anti-Corrosion Pigment Sector
Brazil is leading the way in Latin America’s anti-corrosion pigment market, holding a 40% share of the region’s market. The country’s strong manufacturing industry and extensive coastline infrastructure create a significant need for protective coatings.
Key Factors Driving Growth in Brazil:
- Large-scale infrastructure development projects, such as:
- Port modernization initiatives
- Expansion of offshore oil platforms
- Railway network improvements
- Growing automotive manufacturing industry
- Increased focus on renewable energy installations
The Brazilian government’s commitment to infrastructure development through the Growth Acceleration Program (PAC) has allocated $65 billion for new construction projects, creating significant opportunities for anti-corrosion pigment manufacturers.
Brazilian manufacturers have developed specialized anti-corrosion solutions for the unique challenges posed by the country’s tropical climate and coastal conditions. These innovations have attracted international partnerships, with companies like Petrobras collaborating with global coating manufacturers to develop high-performance protective solutions.
Investment opportunities in Brazil’s anti-corrosion pigment sector continue to expand, driven by:
- Growing demand from neighboring countries
- Technological advancements in local manufacturing
- Strategic location for serving South American markets
- Availability of raw materials and skilled workforce
Future Outlook: Innovations and Market Projections
The anti-corrosion pigment market shows promising growth trajectories, with projections indicating a 3.6% CAGR through 2033. Market analysts predict a substantial shift toward smart coating technologies, incorporating:
- Self-healing coatings utilizing microencapsulation technology
- Graphene-based solutions for enhanced durability
- IoT-integrated coating systems for real-time monitoring
- Nano-engineered particles for superior protection
Reshaping Product Development
R&D investments are reshaping product development, with key innovations focusing on:
- Bio-based alternatives – Plant-derived compounds replacing traditional chemical solutions
- Zero-VOC formulations – Meeting stricter environmental regulations
- Multi-functional coatings – Combining anti-corrosion with additional protective properties
Evolving Technological Landscape
The market’s technological landscape is evolving through:
- AI-driven formulation optimization
- Advanced polymer science applications
- Sustainable raw material sourcing
- Enhanced application methods
Anticipated Market Growth
Industry experts anticipate a $54.06 billion market value by 2034, driven by emerging technologies and increased infrastructure spending. Research facilities are prioritizing the development of cost-effective solutions that maintain high-performance standards while reducing environmental impact.
Current R&D Focus Areas
Current R&D focus areas include:
- Quantum dot technology integration
- Advanced ceramic-based pigments
- Hybrid organic-inorganic compounds
- Smart sensing capabilities
Competitive Landscape: Major Industry Players
The anti-corrosion pigment market has several key players who are influencing the industry through strategic actions and technological advancements:
-
PPG Industries, Inc. – United States
-
Akzonobel N.V. – Netherlands
-
The Sherwin-Williams Company – United States
-
Jotun – Norway
-
Kansai Paint Co., Ltd. – Japan
-
Axalta Coating Systems Ltd. – United States
-
BASF SE – Germany
-
Hempel A/S – Denmark
-
RPM International Inc. – United States
-
Nippon Paint Holdings Co., Ltd. – Japan
Overall
Report Metric | Details |
---|---|
Report Name | Global Anti-Corrosion Pigment Market Report |
Base Year | 2024 |
Segment by Type |
|
Segment by Application |
|
Geographies Covered |
|
Forecast units | USD million in value |
Report coverage | Revenue and volume forecast, company share, competitive landscape, growth factors and trends |
The anti-corrosion pigment market is at a critical point, with expected growth to $37.9 billion by 2025 showing the industry’s strength and potential. This growth is driven by three main factors:
1. Infrastructure Development
- Major investments in developing countries
- Replacement of aging infrastructure in developed nations
- Increasing demands from urbanization
2. Technological Innovation
- Development of smart coatings
- Breakthroughs in eco-friendly formulations
- Solutions for enhanced durability
3. Regional Market Dynamics
- Continued dominance of the Asia-Pacific region
- Stability of the U.S. market through infrastructure projects
- Potential of Brazil’s emerging market
The industry is undergoing transformation due to sustainability requirements and integration of digital technology. Companies that invest in research and development (R&D) and adopt environmentally friendly technologies are positioning themselves for success in this changing landscape.
Market participants should focus on:
- Developing sustainable coating solutions
- Expanding presence in emerging markets
- Building strategic partnerships
- Investing in advanced manufacturing capabilities
The anti-corrosion pigment sector is crucial for protecting global infrastructure. Its growth trajectory reflects both immediate market needs and long-term industrial development, creating opportunities for innovation and market expansion in various regions.
Global Anti-Corrosion Pigment Market Report(Can Read by Free sample)–Table of Contents
Chapter 1:Anti-Corrosion Pigment Market Analysis Overview
- Competitive Forces Analysis(Porter’s Five Forces)
- Strategic Growth Assessment(Ansoff Matrix)
- Industry Value Chain Insights
- Regional Trends and Key Market Drivers
- Anti-Corrosion Pigment Market Segmentation Overview
Chapter 2:Competitive Landscape
- GlobalAnti-Corrosion Pigment Players and Regional Insights
- Key Players and Market Share Analysis
- Sales Trends of Leading Companies
- Year-on-Year Performance Insights
- Competitive Strategies and Market Positioning
- Key Differentiators and Strategic Moves
Chapter 3:Anti-Corrosion Pigment Market Segmentation Analysis
- Key Data and Visual Insights
- Trends,Growth Rates,and Drivers
- Segment Dynamics and Insights
- Detailed Market Analysis by Segment
Chapter 4:Regional Market Performance
- Consumer Trends by Region
- Historical Data and Growth Forecasts
- Regional Growth Factors
- Economic,Demographic,and Technological Impacts
- Challenges and Opportunities in Key Regions
- Regional Trends and Market Shifts
- Key Cities and High-Demand Areas
Chapter 5:Anti-Corrosion Pigment Emerging and Untapped Markets
- Growth Potential in Secondary Regions
- Trends,Challenges,and Opportunities
Chapter 6:Product and Application Segmentation
- Product Types and Innovation Trends
- Application-Based Market Insights
Chapter 7:Anti-Corrosion Pigment Consumer Insights
- Demographics and Buying Behaviors
- TargetAudience Profiles
Chapter 8:Key Findings and Recommendations
- Summary of Anti-Corrosion Pigment Market Insights
Actionable Recommendations for Stakeholders
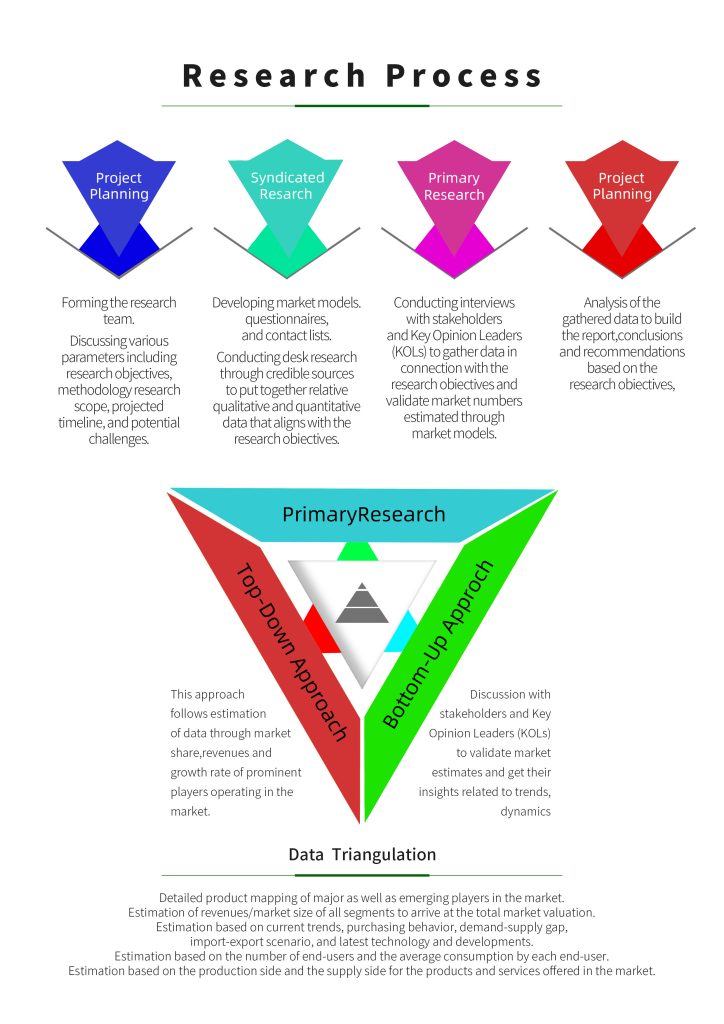
Access the study in MULTIPLEFORMATS
Didn’t find what you’re looking for?
TALK TO OUR ANALYST TEAM
Need something within your budget?
NO WORRIES! WE GOT YOU COVERED!
Call us on: +1-866-739-3133
Email: infor@wkinformation.com
What is the projected growth rate of the anti-corrosion pigment market from 2023 to 2033?
The anti-corrosion pigment market is expected to experience significant growth over the next decade, driven by increased infrastructure development and demand for protective coatings.
What are the key raw materials used in the production of anti-corrosion pigments?
Key raw materials for anti-corrosion pigments include zinc, epoxy resins, polyurethane, and various additives that enhance performance and durability.
How do eco-friendly coatings influence the anti-corrosion pigment market?
Current trends show a growing demand for eco-friendly coatings in the anti-corrosion pigment market, as manufacturers innovate to create sustainable solutions that meet environmental regulations.
What challenges do manufacturers face in the anti-corrosion pigment market?
Manufacturers encounter several challenges including regulatory compliance with environmental standards, competition within the market, and addressing environmental concerns related to traditional pigments.
How does geopolitical tension affect the trade of anti-corrosion pigments?
Geopolitical tensions can significantly impact trade policies and tariffs, which in turn affect pricing, availability, and supply chain dynamics in the global anti-corrosion pigment market.
What role does Brazil play in the Latin American anti-corrosion pigment sector?
Brazil is emerging as a key player in the Latin American anti-corrosion pigment sector due to its expanding infrastructure projects and favorable investment opportunities within the region.