Aerospace Defense Ducting Market Forecasted to Hit $481.6 Million by 2025: Strategic Demand in the U.S., France, and Japan
Aerospace Defense Ducting Market to reach $481.6 million by 2025. Analyze the strategic demand driving growth in the U.S., France, and Japan industry.
- Last Updated:
Aerospace Defense Ducting Market in Q1 and Q2 of 2025
The Aerospace Defense Ducting market is projected to hit $481.6 million by 2025, growing at a CAGR of 5.6% through 2033. Q1 earnings are expected to be around $110 million, with Q2 increasing to roughly $122 million, driven by ongoing modernization programs across military aircraft fleets.
Key Players and Contributions
- The U.S. leads the market with extensive investments in hypersonic and stealth platform upgrades that require advanced thermal-resistant ducting systems.
- France’s aerospace suppliers are contributing with composite-based ducting solutions for reduced weight and higher durability.
- Japan’s role is growing through both defense sector development and tight collaboration with U.S. aerospace primes.
Market Trends
The market is increasingly favoring titanium and high-temperature polymer composites for fuel and environmental control systems.
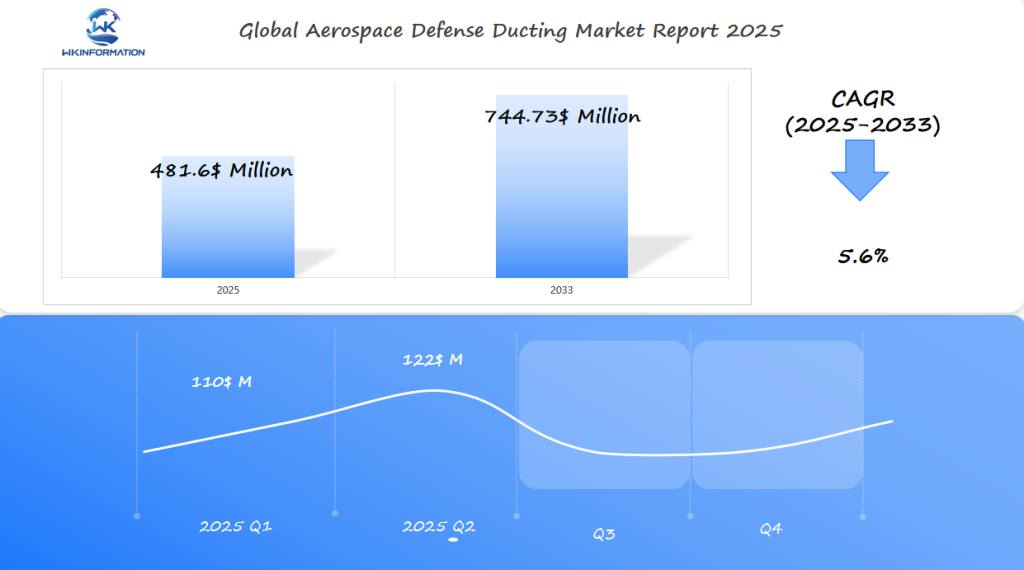
Understanding the Role of Upstream and Downstream Chains in Aerospace Defense Ducting
The complex interaction between upstream and downstream supply chains has a significant impact on the overall Aerospace Defense Ducting Market. The success of this market depends greatly on how well both of these supply chains operate.
Supply chain complexities
The supply chain complexities in the Aerospace Defense Ducting Market are multifaceted, involving the sourcing of raw materials, manufacturing processes, and logistics. These complexities can lead to delays and increased costs, ultimately affecting the market’s growth.
The sourcing of raw materials, for instance, requires careful planning and management due to the specific requirements of the aerospace industry. High-quality materials that meet stringent standards are essential, and any disruptions in their supply can have significant repercussions.
Impact on market growth
The impact of supply chain complexities on market growth is substantial. Some of the key effects include:
- Increased costs due to inefficiencies in the supply chain
- Delays in product delivery, affecting customer satisfaction
- Reduced competitiveness due to higher production costs
To mitigate these effects, companies in the Aerospace Defense Ducting Market are adopting strategies such as diversifying their supplier base and investing in supply chain management technologies.
According to industry experts, “Effective supply chain management is crucial for the success of companies in the Aerospace Defense Ducting Market.” This underscores the importance of addressing supply chain complexities to ensure market growth.
Trends in lightweight composite materials and thermal management
The Aerospace Defense Ducting Market is experiencing a major shift towards the use of lightweight composite materials. This change is being driven by the materials’ high strength-to-weight ratio and ability to withstand extreme temperatures. Improvements in composite materials are crucial in shaping the future of aerospace technology.
Advancements in Composite Materials
Recent developments in composite materials have led to enhanced performance and efficiency in aerospace applications. These materials are engineered to provide superior durability and resistance to environmental factors, making them ideal for use in harsh aerospace environments.
The use of composite materials in ducting systems offers several benefits, including reduced weight, increased flexibility, and improved thermal resistance. This enables aircraft to operate more efficiently and safely.
Thermal Management Solutions
Effective thermal management is critical in aerospace applications, where extreme temperatures can impact system performance and safety. Advanced thermal management solutions are being developed to address these challenges, ensuring that ducting systems can operate within optimal temperature ranges.
Thermal management technologies play a crucial role in maintaining the integrity of aerospace systems, particularly in high-temperature environments. By leveraging these technologies, manufacturers can enhance the reliability and performance of their products.
The integration of lightweight composite materials and advanced thermal management solutions is set to drive innovation in the Aerospace Defense Ducting Market, enabling the development of more efficient and capable aerospace systems.
Restrictions from stringent aerospace compliance and cost burdens
The Aerospace Defense Ducting Market is heavily influenced by strict compliance requirements and the resulting financial implications. Aerospace compliance is not just a regulatory necessity but a critical factor that determines the viability and success of ducting systems in both commercial and defense aviation.
The complexity of aerospace compliance comes from the rigorous standards set by regulatory bodies such as the Federal Aviation Administration (FAA) and the European Aviation Safety Agency (EASA). These organizations enforce strict guidelines to ensure safety, performance, and reliability.
Compliance challenges
Manufacturers face significant challenges in complying with these regulations. For example, the use of lightweight composite materials, which are beneficial for reducing weight and improving fuel efficiency, must still meet strict safety and performance standards. This requires a large investment in research and development.
Cost implications
The financial burden of compliance cannot be overstated. The cost of developing and testing ducting systems that meet aerospace standards is high. Moreover, the cost of non-compliance can be even higher, potentially leading to costly rework, legal penalties, or damage to a company’s reputation.
Cost Factor | Impact on Manufacturers | Potential Solutions |
Research and Development | Increased expenditure to meet compliance standards | Collaboration with regulatory bodies, investment in R&D |
Testing and Certification | High costs associated with testing and obtaining certifications | Streamlining testing processes, early certification planning |
Material Sourcing | Higher costs for compliant materials | Sourcing from certified suppliers, material innovation |
While stringent aerospace compliance and associated cost burdens present significant challenges to the Aerospace Defense Ducting Market, they also drive innovation and improvement in safety and performance standards.
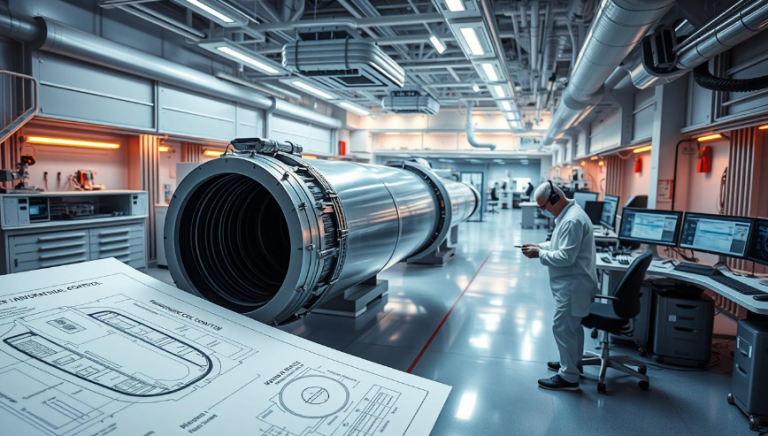
Geopolitical impact on defense aerospace supply routes and materials
Geopolitical instability can disrupt the supply of critical materials in the Aerospace Defense Ducting Market. The complex interplay of global politics and defense needs creates a challenging environment for suppliers and manufacturers.
Geopolitical Influences
The defense aerospace sector is particularly vulnerable to geopolitical tensions. Trade restrictions, sanctions, and conflicts can all impact the availability and cost of raw materials and finished goods. For instance, tensions between major powers can lead to trade wars that affect the supply chain.
Key geopolitical factors influencing the Aerospace Defense Ducting Market include:
- Trade policies and tariffs
- Sanctions and export controls
- Regional conflicts and instability
Impact on Supply Routes
The supply routes for defense aerospace materials are often complex and span multiple countries. Geopolitical instability can lead to the disruption of these routes, causing delays and increased costs. For example, a conflict in a region through which a critical supply route passes can halt the transportation of goods.
The impact on supply routes can be mitigated through:
- Diversification of supply sources
- Development of alternative supply routes
- Strategic stockpiling of critical materials
Companies operating in the Aerospace Defense Ducting Market must navigate this complex geopolitical landscape to ensure a stable supply of materials. This involves closely monitoring geopolitical developments and adapting their supply chain strategies accordingly.
The geopolitical impact on defense aerospace supply routes and materials is a critical factor that companies must consider when planning their supply chain strategies. By understanding these dynamics, businesses can better navigate the challenges and opportunities in the Aerospace Defense Ducting Market.
Type segmentation: rigid, flexible, and semi-rigid ducting
Aerospace defense ducting is not a one-size-fits-all solution; it encompasses rigid, flexible, and semi-rigid types, each with unique applications and advantages. The diversity in ducting systems is crucial for meeting the complex demands of modern aerospace defense projects.
The categorization into rigid, flexible, and semi-rigid ducting is based on the material properties and the specific requirements of different aerospace applications. Rigid ducting is often used where high durability and resistance to extreme temperatures are required.
Rigid Ducting Applications
Rigid ducting systems are mainly used in high-temperature areas of aircraft and defense vehicles, such as near engines or in exhaust systems. Their ability to maintain structural integrity under stress makes them ideal for these critical applications.
Flexible and Semi-Rigid Ducting Uses
Flexible ducting is used in applications where flexibility and ease of installation are crucial. It is commonly found in environmental control systems and other areas where ducting needs to navigate complex shapes.
Semi-rigid ducting offers a balance between the durability of rigid ducting and the flexibility of flexible ducting, making it suitable for a wide range of aerospace applications.
The choice between rigid, flexible, and semi-rigid ducting depends on the specific requirements of the aerospace application, including factors such as temperature resistance, durability, and installation constraints.
Application areas: airframes, engines, and environmental control systems
Aerospace defense ducting is essential for the operation of airframes, engines, and environmental control systems in modern aircraft. These systems are crucial for the overall performance and safety of the aircraft, and ducting plays a critical role in their functioning.
Airframe applications
In airframes, ducting is used to manage airflow and pressure, ensuring that the structural integrity of the aircraft is maintained. Efficient ducting systems help in reducing weight and enhancing the overall aerodynamics of the aircraft.
“The use of advanced materials and designs in ducting systems has significantly improved the performance of modern aircraft,” says an industry expert. This highlights the importance of continuous innovation in aerospace defense ducting.
Engine and environmental control system applications
Engines and environmental control systems (ECS) are other critical areas where aerospace defense ducting is applied. In engines, ducting is used to direct airflow and manage thermal loads, while in ECS, it helps in maintaining a controlled environment within the aircraft.
- In engines, ducting enhances performance and efficiency.
- In ECS, ducting ensures a stable and comfortable cabin environment.
The use of lightweight and heat-resistant materials in ducting systems for engines and ECS is crucial for improving aircraft performance and reducing maintenance costs.
As the aerospace industry continues to evolve, the demand for advanced ducting systems that can meet the complex requirements of modern aircraft is expected to grow. Manufacturers are focusing on developing innovative solutions that can provide enhanced performance, reliability, and efficiency.
Global adoption in military aviation and defense projects
Advanced ducting systems are becoming a critical component in military aviation and defense projects globally. The increasing complexity of modern military aircraft and the need for enhanced performance and efficiency are driving the demand for sophisticated aerospace defense ducting solutions.
Military Aviation Applications
The use of advanced ducting systems in military aviation is enhancing the overall performance of aircraft. These systems are crucial for managing airflow, temperature, and pressure within the aircraft, ensuring optimal operational conditions.
Defense Project Implementations
Defense projects around the world are incorporating advanced ducting systems to improve the capabilities of their military aircraft. For instance, the development of next-generation fighter jets and transport aircraft relies heavily on the integration of high-performance ducting systems.
The adoption of aerospace defense ducting in military aviation is not limited to new aircraft designs. Existing fleets are also being upgraded with advanced ducting systems to enhance their performance and extend their service life. This trend is driven by the need for improved efficiency, reduced maintenance costs, and enhanced operational capabilities.
Key Benefits of Advanced Ducting Systems:
- Improved thermal management
- Enhanced airflow control
- Increased durability and resistance to extreme conditions
- Reduced weight and increased flexibility
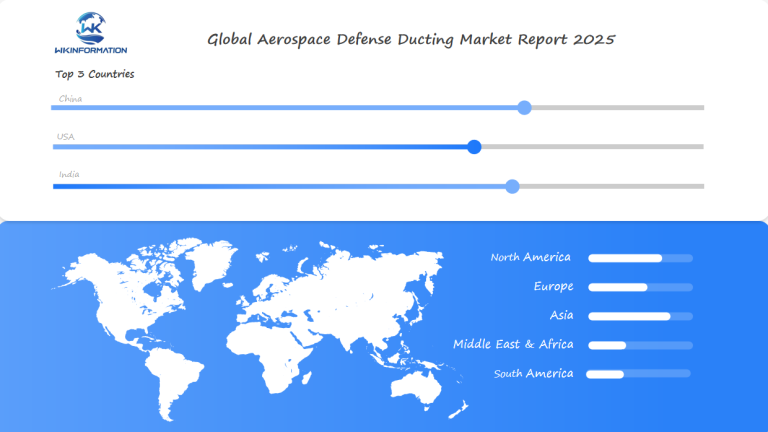
U.S. Leadership in Aerospace Component Manufacturing
The U.S. aerospace industry is a powerhouse, driving growth and development in the global aerospace defense ducting market. With its advanced manufacturing capabilities and technological expertise, the country has established itself as a leader in the production of high-quality aerospace components.
Aerospace Industry Overview
The U.S. aerospace industry has a strong presence in both domestic and international markets. It is supported by a network of manufacturers, suppliers, and research institutions that work together to innovate and improve aerospace technologies.
Key factors contributing to the U.S. leadership include:
- Advanced manufacturing technologies
- Highly skilled workforce
- Strong research and development infrastructure
- Favorable business environment
Leadership in Component Manufacturing
The U.S. is known for its expertise in manufacturing aerospace components, such as ducting systems. The country’s manufacturers have developed cutting-edge technologies that allow them to produce complex components with high precision and reliability.
The U.S. maintains its leadership in aerospace component manufacturing by being flexible and responsive to changing market demands and technological advancements. This positions the country for continued success in the global aerospace defense ducting market.
France’s Integrated Role in EU Aerospace Defense Collaboration
France’s involvement in EU aerospace defense collaboration is a crucial factor in the development of advanced aerospace technologies, including ducting systems. This collaboration not only enhances the competitiveness of the European aerospace industry but also fosters innovation in critical areas such as lightweight composite materials and thermal management.
EU Aerospace Defense Collaboration
The European Union’s aerospace defense collaboration is a multifaceted initiative aimed at strengthening the continent’s defense capabilities. France, as a key player, contributes significantly to this effort by sharing its expertise and resources. This collaborative approach enables the development of cutting-edge aerospace technologies that are crucial for modern defense systems.
France’s Role in the Collaboration
France’s role in EU aerospace defense collaboration is multifaceted. It involves participating in joint research projects, sharing technological advancements, and collaborating on the production of advanced aerospace components. France’s leadership in this area has been instrumental in driving the development of sophisticated ducting systems that are used in various aerospace applications.
EU aerospace defense collaboration
The collaboration between France and other EU member states has led to significant advancements in aerospace defense technologies. It has also created new opportunities for European companies to compete in the global market, particularly in the area of aerospace defense ducting.
Japan’s focus on stealth aircraft and high-performance systems
With a focus on technological advancement, Japan is investing heavily in the development of stealth aircraft and high-performance systems. This investment is driven by the need for advanced aerospace technologies that can provide a strategic edge in modern defense systems.
The development of stealth aircraft technology is a significant area of focus for Japan’s aerospace industry. Stealth technology involves designing aircraft to minimize their radar cross-section, making them harder to detect. This is achieved through the use of advanced materials and designs that absorb or scatter radar waves.
Stealth aircraft technology
Japan is working on creating stealth aircraft that can avoid being detected. This involves not only designing the aircraft but also creating advanced materials and systems that can handle the challenges of flying while still being stealthy.
High-performance system developments
One important part of Japan’s aerospace industry is making high-performance systems that can meet the needs of stealth aircraft. These systems include:
- powerful engines
- complex electronic systems
- efficient climate control systems
It’s essential to combine these high-performance systems with stealth aircraft technology for Japan’s aerospace projects to succeed. This requires a thorough understanding of both the technical and operational needs of these advanced systems.
Future advancements in heat-resistant and radar-absorbing ducting
Research into heat-resistant and radar-absorbing materials is leading to the development of the next generation of aerospace defense ducting. These advancements are essential for improving the performance and stealth capabilities of modern aircraft.
Heat-resistant ducting developments
The development of heat-resistant ducting is a significant area of research, driven by the need for materials that can withstand extreme temperatures. Advanced composites and ceramics are being explored for their potential to provide the necessary thermal resistance.
These materials not only improve the durability of ducting systems but also contribute to the overall efficiency of aircraft engines. By withstanding higher temperatures, heat-resistant ducting enables more efficient engine performance, which is critical for both military and commercial aviation.
Radar-absorbing ducting technologies
Radar-absorbing ducting technologies are another key area of innovation. Radar-absorbing materials (RAMs) are being integrated into ducting systems to reduce the radar cross-section of aircraft, thereby enhancing their stealth capabilities.
The integration of RAMs into ducting involves complex engineering challenges, including maintaining the structural integrity of the ducting while ensuring effective radar absorption. Advances in this area are expected to significantly impact the design of future aircraft.
Material | Heat Resistance | Radar Absorption |
Advanced Composites | High | Moderate |
Ceramic Materials | Very High | Low |
RAM-integrated Composites | High | High |
The table above illustrates the varying characteristics of materials being researched for heat-resistant and radar-absorbing ducting. As research progresses, the development of materials that balance both heat resistance and radar absorption is expected to drive significant advancements in aerospace defense technology.
Competitor strategies in ducting system innovation
Competitor strategies in ducting system innovation—particularly within aerospace, HVAC, automotive, and industrial applications—are shaped by demands for performance, weight reduction, cost efficiency, and sustainability.
- Eaton – United States
- GE Aviation – United States
- Safran – France
- Honeywell – United States
- Moog – United States
- Senior Aerospace – United Kingdom
- Triumph Group – United States
- Woodward – United States
- Meggitt – United Kingdom
- Hexcel – United States
Overall
Report Metric | Details |
---|---|
Report Name | Global Aerospace Defense Ducting Report |
Base Year | 2024 |
Segment by Type |
· Rigid · Flexible · Semi-Rigid Ducting |
Segment by Application |
· Airframes · Engines · Environmental Control Systems |
Geographies Covered |
· North America (United States, Canada) · Europe (Germany, France, UK, Italy, Russia) · Asia-Pacific (China, Japan, South Korea, Taiwan) · Southeast Asia (India) · Latin America (Mexico, Brazil) |
Forecast units | USD million in value |
Report coverage | Revenue and volume forecast, company share, competitive landscape, growth factors and trends |
The Aerospace Defense Ducting Market is growing due to technological advancements and increased demand from the defense sector. It is expected to reach $481.6 Million by 2025, with growth driven by the use of lightweight composite materials and improvements in thermal management systems.
The market outlook is positive, with ongoing research and development leading to further innovations in aerospace defense ducting. The demand for rigid, flexible, and semi-rigid ducting is expected to rise, driven by their applications in airframes, engines, and environmental control systems.
As the Aerospace Defense Ducting Market continues to grow, industry players are likely to focus on developing heat-resistant and radar-absorbing ducting solutions. This will be crucial in meeting the evolving needs of the defense sector, particularly for stealth aircraft and high-performance systems.
Global Aerospace Defense Ducting Market Report (Can Read by Free sample) – Table of Contents
Chapter 1: Aerospace Defense Ducting Market Analysis Overview
- Competitive Forces Analysis (Porter’s Five Forces)
- Strategic Growth Assessment (Ansoff Matrix)
- Industry Value Chain Insights
- Regional Trends and Key Market Drivers
- Aerospace Defense DuctingMarket Segmentation Overview
Chapter 2: Competitive Landscape
- Global Aerospace Defense Ductingplayers and Regional Insights
- Key Players and Market Share Analysis
- Sales Trends of Leading Companies
- Year-on-Year Performance Insights
- Competitive Strategies and Market Positioning
- Key Differentiators and Strategic Moves
Chapter 3: Aerospace Defense Ducting Market Segmentation Analysis
- Key Data and Visual Insights
- Trends, Growth Rates, and Drivers
- Segment Dynamics and Insights
- Detailed Market Analysis by Segment
Chapter 4: Regional Market Performance
- Consumer Trends by Region
- Historical Data and Growth Forecasts
- Regional Growth Factors
- Economic, Demographic, and Technological Impacts
- Challenges and Opportunities in Key Regions
- Regional Trends and Market Shifts
- Key Cities and High-Demand Areas
Chapter 5: Aerospace Defense Ducting Emerging and Untapped Markets
- Growth Potential in Secondary Regions
- Trends, Challenges, and Opportunities
Chapter 6: Product and Application Segmentation
- Product Types and Innovation Trends
- Application-Based Market Insights
Chapter 7: Aerospace Defense Ducting Consumer Insights
- Demographics and Buying Behaviors
- Target Audience Profiles
Chapter 8: Key Findings and Recommendations
- Summary ofAerospace Defense DuctingMarket Insights
- Actionable Recommendations for Stakeholders
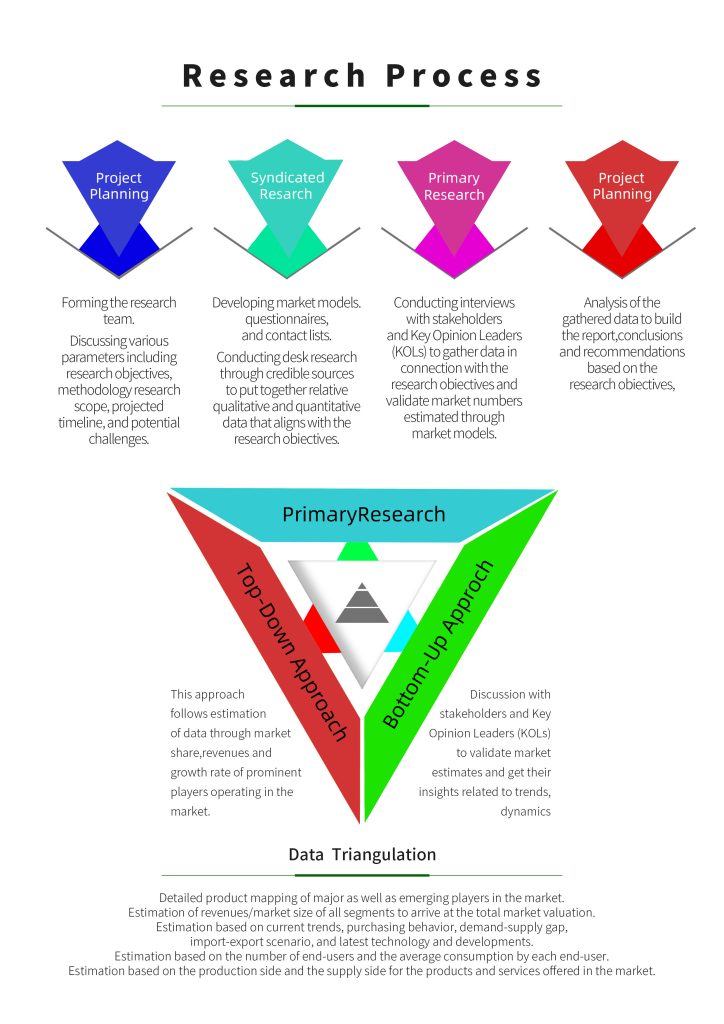
Access the study in MULTIPLEFORMATS
Didn’t find what you’re looking for?
TALK TO OUR ANALYST TEAM
Need something within your budget?
NO WORRIES! WE GOT YOU COVERED!
Call us on: +1-866-739-3133
Email: infor@wkinformation.com
What is the forecasted value of the Aerospace Defense Ducting Market by 2025?
The Aerospace Defense Ducting Market is expected to reach $481.6 million by 2025.
What is driving the growth of the Aerospace Defense Ducting Market?
The growth is driven by advancements in aerospace technology and the need for more efficient ducting systems, particularly in the U.S. defense sector.
What are the complexities in the supply chain of the Aerospace Defense Ducting Market?
The supply chain complexities include sourcing of raw materials and manufacturing processes, which play a significant role in determining market growth.
What is the trend in the use of materials in aerospace defense ducting?
There is a shift towards lightweight composite materials due to their high strength-to-weight ratio and resistance to extreme temperatures.
How do geopolitical tensions affect the Aerospace Defense Ducting Market?
Geopolitical tensions can disrupt supply routes and impact the availability of critical materials.
What are the different types of ducting used in aerospace applications?
The types of ducting used are rigid, flexible, and semi-rigid, each with its specific applications and advantages.
Where is aerospace defense ducting used?
Aerospace defense ducting is used in airframes, engines, and environmental control systems, each with unique requirements and challenges.
How is the U.S. involved in the Aerospace Defense Ducting Market?
The U.S. is a leading manufacturer of aerospace components, including ducting systems, and plays a dominant role in the market.
What is France’s role in the EU aerospace defense collaboration?
France is a key player in EU aerospace defense collaboration efforts, contributing to the development of advanced aerospace technologies.
What is Japan focusing on in terms of aerospace technology?
Japan is investing heavily in stealth aircraft technology and high-performance systems, which require advanced ducting systems.
What are the future advancements expected in aerospace defense ducting?
Research is ongoing into developing heat-resistant and radar-absorbing ducting materials, which will enhance the performance and stealth capabilities of aircraft.