$1.49 Billion Robust Growth in Spindle Repair Market in the U.S., Germany, and Japan by 2025
Explore the comprehensive analysis of the Global Spindle Repair Market, projected to reach USD 2.83 billion by 2033. This report examines key growth drivers, regional trends, and industry challenges, offering valuable insights into market dynamics, competitive landscapes, and future opportunities. Discover how technological advancements, increasing automation, and demand from sectors like automotive and aerospace are shaping this crucial manufacturing industry segment.
- Last Updated:
Spindle Repair Market Q1 and Q2 2025 Forecast
The Spindle Repair market is projected to reach $1.49 billion in 2025, growing at an 8.35% CAGR from 2025 to 2033. In Q1 2025, the market is expected to generate approximately $370 million, driven by the increasing demand for machine tool maintenance, precision repairs, and extended lifespan of spindles used in high-performance machinery in the U.S., Germany, and Japan. The need to minimize downtime and improve production efficiency is contributing to the growth of this market.
By Q2 2025, the market is forecasted to reach $390 million, supported by advanced diagnostic tools, AI-driven repair techniques, and cost-effective repair services. The U.S. leads in industrial manufacturing and equipment repairs, Germany continues to focus on precision engineering, and Japan is focusing on robotics and automation-driven spindle repairs. As the demand for higher productivity and minimized operational interruptions grows, the spindle repair market is poised for sustained growth.
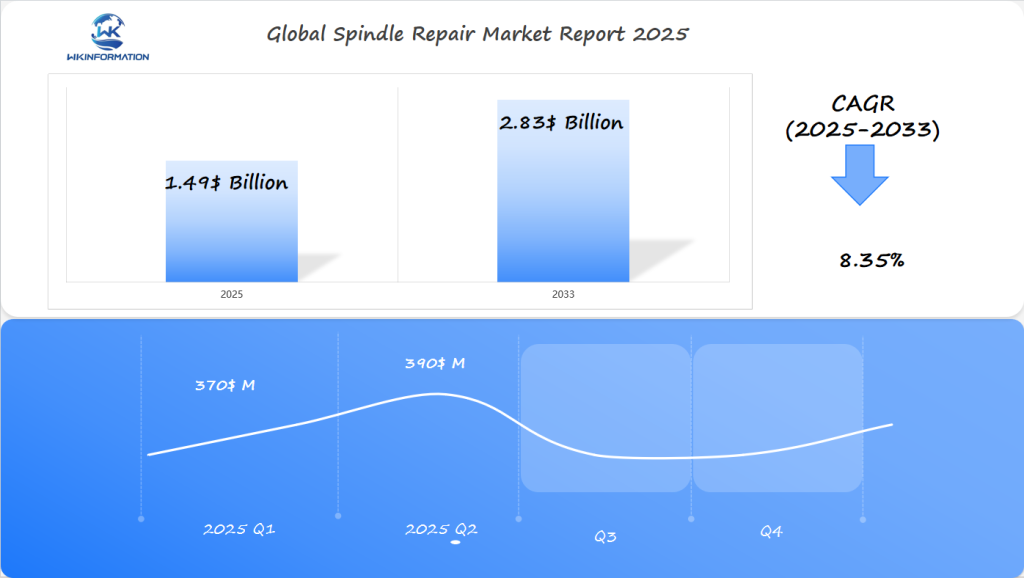
Understanding the Spindle Repair Industry: Upstream and Downstream
The spindle repair industry is crucial for maintaining the smooth operation of industrial machinery. It connects various sectors, with suppliers and users collaborating to ensure the manufacturing process runs efficiently.
To understand the spindle repair supply chain, we need to examine its key components and stakeholders who play a role in keeping machinery in optimal condition.
Upstream Components and Suppliers
Upstream suppliers are essential for spindle repair. They make parts needed for machines to work well:
- Precision bearings from advanced metallurgy companies
- High-performance motor manufacturers
- Specialized lubrication system providers
- Precision engineering component suppliers
Downstream Applications and End-Users
The downstream part of the supply chain serves many industries. These industries need advanced machinery maintenance:
Industry Sector | Spindle Repair Critical Requirements |
Automotive Manufacturing | High-precision machining centers |
Aerospace Engineering | Extreme tolerance mechanical systems |
Electronics Production | Micro-precision spindle capabilities |
Medical Device Manufacturing | Contamination-free repair processes |
Maintaining industrial machinery needs a detailed approach. It involves using advanced tools, precision engineering, and knowing complex systems well.
Technological Advances in Spindle Repair
The world of spindle repair is changing fast. New ways to diagnose and maintain equipment are leading the way. These advancements are making machines work better and last longer.
Spindle repair is getting a big boost in many industries. Thanks to smart algorithms and monitoring systems, problems can be spotted before they start. This means less downtime and more productivity.
Predictive Maintenance Technologies
Predictive maintenance is a game changer in spindle repair. It’s made possible by:
- Real-time vibration analysis
- Machine learning diagnostic algorithms
- Wireless sensor networks
- Advanced data collection systems
Advanced Diagnostic Tools
New diagnostic tools are making spindle repair more precise and quick. They help find issues fast, cutting down on maintenance costs and downtime.
Diagnostic Tool | Key Features | Performance Impact |
Thermal Imaging | Non-invasive temperature mapping | Early wear detection |
Acoustic Emission Sensors | High-frequency sound analysis | Microscopic defect identification |
Spectral Analysis Equipment | Comprehensive frequency monitoring | Precise mechanical condition assessment |
By using these advanced tools, manufacturers can make their equipment more reliable and efficient. Predictive maintenance is now a must for staying ahead in the game.
Challenges in Spindle Repair Services
The spindle repair industry is facing big challenges. These come from two main areas: not enough workers and complex technology.
Spindle repair has gotten much harder lately. This puts a lot of pressure on the workers. They need advanced skills and deep technical knowledge because of the fast-changing manufacturing world.
Skilled Labor Shortage
The workforce for spindle repair is facing a big skills gap. Key problems include:
- An aging workforce with specialized skills
- Not enough technical training programs
- Younger people are less interested in manufacturing maintenance careers
Increasing Complexity of Modern Spindles
Modern spindles are very complex. They need advanced skills to diagnose and repair. Technicians must deal with complex mechanical and electronic systems.
Spindle Complexity Factor | Impact on Repair Services |
Advanced Materials | Requires specialized knowledge of metallurgy |
Integrated Electronics | Demands comprehensive understanding of digital systems |
Precision Engineering | Necessitates extremely precise diagnostic and repair techniques |
To tackle these challenges, we need to invest in training and partnerships. We must work together with schools and companies to improve the workforce.
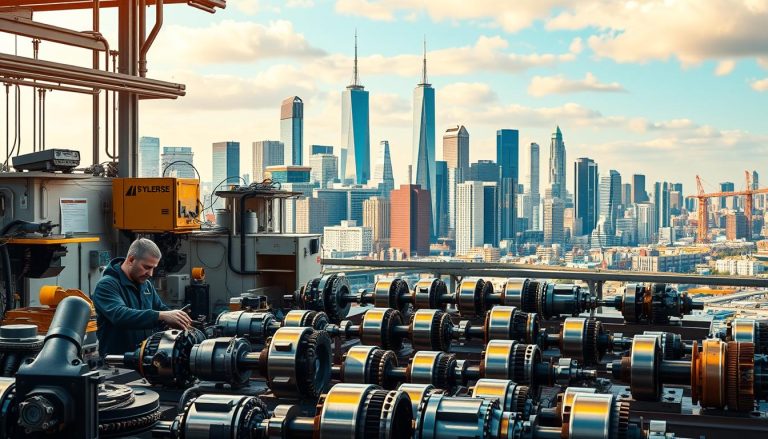
Geopolitical Influence on the Spindle Repair Industry
The spindle repair global market is facing big challenges from global politics. Trade policies and supply chain issues are changing how we trade and repair industrial equipment. This forces companies to quickly adjust to new global rules.
Global politics are causing big waves in the spindle repair world. The way countries work together affects how we get parts, how much it costs, and how we fix things.
Trade Policies and Tariffs: Economic Pressures
Recent trade changes have really hit the spindle repair market hard. The main issues are:
- More rules on moving goods across borders
- Changes in tariffs on industrial parts
- Tougher rules for buying and selling things internationally
“The industrial equipment trade is experiencing unprecedented volatility due to geopolitical uncertainties.” – Manufacturing Industry Analyst
Global Supply Chain Disruptions
Keeping supply chains strong is key for spindle repair services. Companies are coming up with smart plans to deal with problems.
Region | Supply Chain Strategy | Adaptation Level |
United States | Domestic Manufacturing Expansion | High |
Germany | Diversified Supplier Networks | Very High |
Japan | Advanced Technological Integration | Moderate |
The world is always changing, and the spindle repair industry needs to keep up. Companies must stay flexible to handle these complex global issues well.
Types of Spindle Repair Services
Industrial equipment requires a comprehensive repair plan. Companies employ specialized repair techniques to ensure optimal machine performance and minimize downtime. The spindle repair industry offers a wide range of services tailored to various needs and equipment conditions.
Effective spindle repair services incorporate several crucial maintenance procedures. These procedures address specific equipment issues and extend the lifespan of machines.
Preventive Maintenance
Preventive maintenance is a proactive approach to maintaining industrial equipment. It involves:
- Conducting regular inspections to identify issues early on
- Scheduling planned inspections
- Ensuring proper lubrication techniques are followed
- Performing alignment tests as needed
“Preventive maintenance can reduce unexpected equipment failures by up to 70%,” say maintenance experts.
Emergency Repairs
When a spindle suddenly fails, quick action is key. Emergency repair services offer:
- 24/7 help from experts
- Quick problem-solving
- Fast repair actions
- Less time lost in production
Rebuilds and Upgrades
Spindle repair services also include full rebuilds and updates. These steps bring equipment close to its original state and add new tech.
By using these advanced repair services, companies can make their equipment last longer and work better. Smart maintenance plans help keep production going and save money on replacing equipment.
Applications of Spindle Repair in Manufacturing
Spindle repair is key in keeping industrial manufacturing running smoothly. These parts are vital for high-precision work. They help ensure top performance and efficiency in complex settings.
Many manufacturing sectors need precision spindle systems to stay efficient. Spindle upkeep is crucial in these fields:
Automotive Manufacturing
In car making, spindle repair is vital for quality. Precision machining centers use spindles to make engine parts and more. This is essential for high-quality car production.
- Engine block manufacturing
- Precision cutting and milling operations
- Advanced robotics integration
Aerospace Sector
The aerospace industry requires utmost accuracy in its operations. Spindle repair plays a crucial role in ensuring that intricate machinery continues to function smoothly. This machinery is responsible for producing lightweight yet durable components used in aircraft and spacecraft.
“In aerospace, a single spindle failure can compromise entire production lines and safety protocols.” – Manufacturing Engineering Magazine
Electronics Manufacturing
Electronics require extreme precision, making spindle maintenance crucial in this industry. Both semiconductors and circuit boards rely on exact spindle systems for their production.
Key Applications of Spindle Systems in Electronics Manufacturing
- Microchip production equipment
- Printed circuit board manufacturing
- Precision semiconductor fabrication
Effective spindle repair strategies minimize downtime and enhance quality, enabling manufacturers to remain competitive in challenging global markets.
Global Spindle Repair Market: Trends and Growth
The global spindle repair market is changing fast. This is thanks to new technologies and the need for better maintenance. Factories around the world are now focusing more on keeping their equipment in top shape.
Spindle repair is growing in many industries. Companies are seeing how important it is to keep their machines running smoothly. This helps them work better and more efficiently.
Market Size and Projections
Experts say the spindle repair market is looking up. It’s expected to hit big numbers in the next few years. This is good news for those in the business.
Key Growth Drivers
- Increasing automation in manufacturing processes
- Rising demand for high-precision industrial components
- Technological advancements in diagnostic tools
- Growing adoption of predictive maintenance strategies
New technologies are changing how we do maintenance. Machine learning and AI are making repairs faster and cheaper. This is a big step forward.
The future of spindle repair lies in proactive, data-driven maintenance strategies that minimize downtime and maximize operational efficiency, such as those outlined in this research article which discusses the benefits of such approaches.
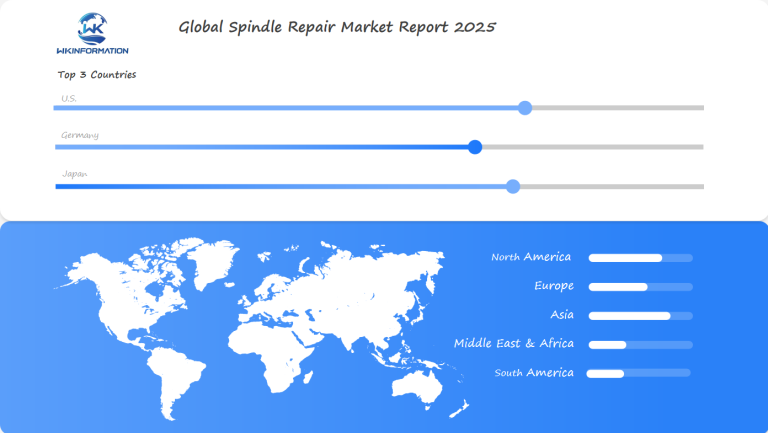
U.S. Spindle Repair Market: Demand and Innovation
The U.S. spindle repair market is an important part of industrial maintenance. It drives technological advancements and helps the economy grow. Manufacturers in the U.S. understand that they need accurate spindle repairs to stay competitive.
Here are some factors contributing to the demand and innovation in the U.S. spindle repair market:
- Rapid integration of technology in industrial maintenance processes
- Increasing need for predictive maintenance solutions
- Growing complexity of manufacturing equipment
Market Size and Key Players
The American industrial maintenance sector has seen big growth in spindle repair services. Top companies are putting a lot into new diagnostic tech and training workers.
Technological Innovations in the U.S. Market
New tech is changing the U.S. spindle repair market. Artificial intelligence and Internet of Things (IoT) are making diagnostics more accurate. This leads to better predictive maintenance.
Companies are tackling the problem of not enough skilled workers. They’re creating advanced diagnostic tools. These tools cut down on manual work and make equipment more effective.
Germany's Spindle Repair Market: Strengths and Developments
The German spindle repair market is a world leader in precision engineering and maintenance. Germany’s manufacturing sector is known for its top-notch technical skills and drive for new technology.
In Europe, German engineering greatly influences industrial maintenance. German makers have created advanced spindle repair methods. These methods are a high standard for quality and performance worldwide.
German Engineering Excellence in Spindle Repair
Key strengths of the German spindle repair market include:
- Cutting-edge diagnostic technologies
- Highly trained technical specialists
- Precision-focused repair methodologies
- Advanced quality control processes
Industry 4.0 and Spindle Repair Innovations
German manufacturers lead in smart maintenance with Industry 4.0 technologies. These innovations bring:
- Real-time monitoring of spindle performance
- Predictive maintenance algorithms
- Automated diagnostic systems
- Enhanced repair efficiency
Digital technologies have changed how spindles are repaired. Now, maintenance is more proactive and smart. This reduces downtime and boosts equipment performance.
German engineering continues to set global benchmarks in precision industrial maintenance and technological innovation.
Japan's Spindle Repair Industry: Precision and Innovation
The Japanese spindle repair market leads the world in industrial maintenance. It’s known for its unmatched precision and innovation. Japan’s manufacturing sector is famous for its detailed approach to machinery upkeep and cutting-edge tech.
Japan’s efforts in technology have changed Asian industrial maintenance a lot. The country’s focus on innovation has made spindle repair better and more efficient worldwide.
Japanese Manufacturing Traditions
Japanese manufacturing values a few key things in maintenance:
- Kaizen philosophy of continuous improvement
- Extreme precision in mechanical engineering
- Rigorous quality control processes
- Long-term equipment reliability focus
Robotics and Automation in Spindle Repair
Japan’s technology has transformed spindle repair through the use of robotics and automation. Advanced diagnostic tools and automated systems are revolutionizing equipment maintenance.
Some major innovations in Japan’s spindle repair industry include:
- AI-powered predictive maintenance systems
- Robotic diagnostic and repair technologies
- Real-time monitoring of spindle performance
- Integrated machine learning algorithms
These technological advancements address the challenges posed by Japan’s aging workforce while upholding the country’s reputation for manufacturing excellence.
Future Trends in Spindle Repair: Automation and Efficiency
The spindle repair industry is about to undergo a significant transformation, thanks to new technologies in industrial maintenance. Manufacturers are now leveraging the latest tech to enhance their diagnostic and operational processes.
These emerging trends in spindle repair are revolutionizing traditional methods by incorporating smart systems that can monitor, diagnose, and repair industrial equipment. This represents a major advancement in the field.
AI and Machine Learning in Diagnostics
Artificial intelligence is making spindle repair diagnostics much better. Some key things include:
- Advanced predictive maintenance algorithms
- Real-time performance monitoring
- Automated fault detection systems
Machine learning can now look at complex vibration patterns. It can predict failures with great accuracy. This means less unexpected downtime.
Remote Monitoring and Repair
The future of spindle maintenance is connected. Manufacturers are making IoT-enabled diagnostic platforms. These platforms let engineers:
- Watch spindle performance from anywhere
- Do virtual diagnostics
- Take quick action
These new technologies are making maintenance faster and more efficient. They’re creating a better repair system.
Competitive Overview: Key Players in the Spindle Repair Market
The spindle repair market is filled with many industrial maintenance providers. They all aim to be the top in their field. Specialized companies play a big role in helping factories work better in many areas.
The world market has big companies and local experts. Each brings something special to fixing machines.
Global Market Leaders:
- PDS – United States
- SKF – Sweden
- Superior Spindle Service – United States
- C&M Precision Spindle – United States
- Precision Spindle & Accessories – United States
- GTI Spindle Technology – United States
- Mazak Corporation – Japan
- CNC Repair (UK) – United Kingdom
- Billor McDowell – United States
- Gilman Precision – United States
Overall
Report Metric | Details |
---|---|
Report Name | Global Spindle Repair Market Report |
Base Year | 2024 |
Segment by Type |
|
Segment by Application |
|
Geographies Covered |
|
Forecast units | USD million in value |
Report coverage | Revenue and volume forecast, company share, competitive landscape, growth factors and trends |
The spindle repair market is key in industrial maintenance, with big economic effects. As manufacturing tech gets better, the spindle repair market keeps changing many industries. Companies see the value in keeping equipment running well and cutting downtime.
There are more chances for growth in industrial maintenance, leading to new tech and jobs. New repair methods help make equipment last longer, save money, and boost production. Small and medium businesses can use these advances to grow, with better tools and plans for upkeep.
The future of spindle repair looks bright, with more growth in precision making. The auto, aerospace, and electronics fields are spending on advanced repair methods to avoid stops in production. New tech like AI for checking and watching equipment from afar will change how we fix things.
Investing in spindle repair will bring big economic wins. Strong maintenance systems help make more, spend less, and create jobs. The growth of spindle repair tech is changing how we keep things running worldwide.
Global Spindle Repair Market Report (Can Read by Free sample) – Table of Contents
Chapter 1: Spindle Repair Market Analysis Overview
- Competitive Forces Analysis (Porter’s Five Forces)
- Strategic Growth Assessment (Ansoff Matrix)
- Industry Value Chain Insights
- Regional Trends and Key Market Drivers
- Spindle Repair Market Segmentation Overview
Chapter 2: Competitive Landscape
- Global Spindle Repairplayers and Regional Insights
- Key Players and Market Share Analysis
- Sales Trends of Leading Companies
- Year-on-Year Performance Insights
- Competitive Strategies and Market Positioning
- Key Differentiators and Strategic Moves
Chapter 3: Spindle Repair Market Segmentation Analysis
- Key Data and Visual Insights
- Trends, Growth Rates, and Drivers
- Segment Dynamics and Insights
- Detailed Market Analysis by Segment
Chapter 4: Regional Market Performance
- Consumer Trends by Region
- Historical Data and Growth Forecasts
- Regional Growth Factors
- Economic, Demographic, and Technological Impacts
- Challenges and Opportunities in Key Regions
- Regional Trends and Market Shifts
- Key Cities and High-Demand Areas
Chapter 5: Spindle Repair Emerging and Untapped Markets
- Growth Potential in Secondary Regions
- Trends, Challenges, and Opportunities
Chapter 6: Product and Application Segmentation
- Product Types and Innovation Trends
- Application-Based Market Insights
Chapter 7: Spindle Repair Consumer Insights
- Demographics and Buying Behaviors
- TargetAudience Profiles
Chapter 8: Key Findings and Recommendations
- Summary of Spindle Repair Market Insights
- Actionable Recommendations for Stakeholders
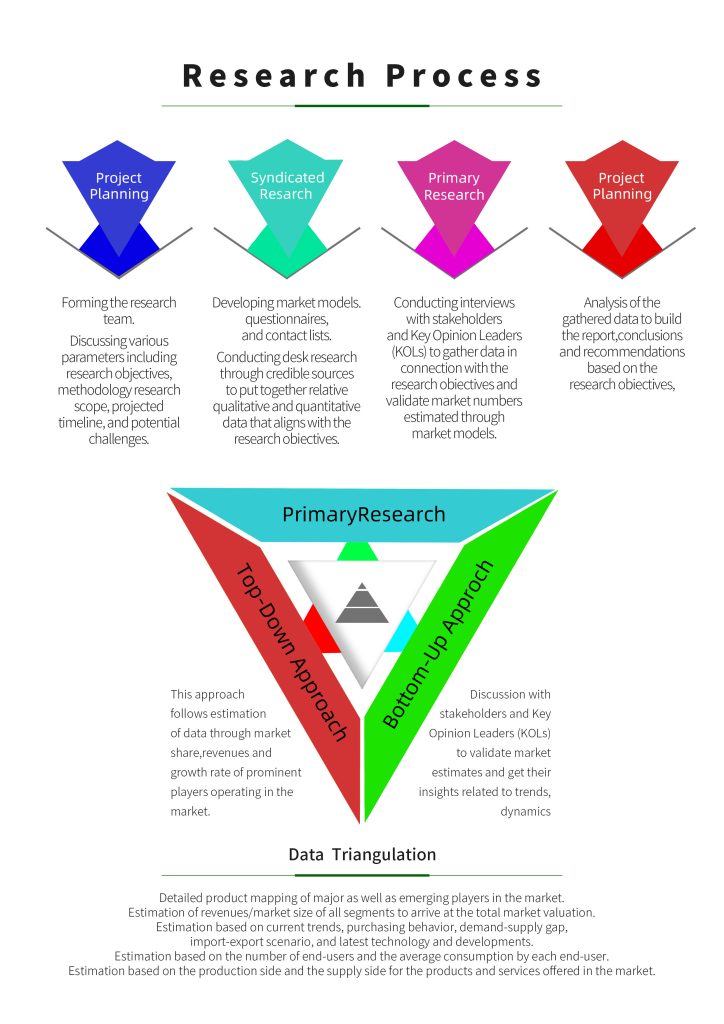
Access the study in MULTIPLEFORMATS
Didn’t find what you’re looking for?
TALK TO OUR ANALYST TEAM
Need something within your budget?
NO WORRIES! WE GOT YOU COVERED!
Call us on: +1-866-739-3133
Email: infor@wkinformation.com
What is driving the growth of the spindle repair market?
The spindle repair market is growing fast. This is because of more automation in making things, a need for precise parts, and the use of CNC machines. Also, keeping production running smoothly in car, plane, and electronics making is key.
How are technological advances impacting spindle repair?
New technologies like predictive maintenance and machine learning are transforming spindle repair. These tools help predict when spindles might fail, quickly address issues, and extend the lifespan of machines.
What are the main challenges in the spindle repair industry?
The major challenges include:
- A shortage of skilled workers
- Increasing complexity of spindles
- The need for continuous learning
This is because the manufacturing process today is different from what it used to be.
What types of spindle repair services are available?
There are many services like regular checks, fixing spindles when they break, rebuilding them, and upgrading. These help keep machines working well and last longer.
How do different regions approach spindle repair?
Each area has its own way:
- The U.S. focuses on new tech and IoT.
- Germany is all about engineering and Industry 4.0.
- Japan uses its precision and robotics to improve spindle repair.
What role does predictive maintenance play in spindle repair?
Predictive maintenance uses AI and machine learning to spot problems before they happen. This lets makers plan maintenance, cut down on unplanned stops, and make equipment work better.
How are geopolitical factors affecting the spindle repair market?
Global politics, such as trade rules and supply chain issues, have a significant impact on the market. In response, companies are:
- Finding new ways to manufacture products
- Investing in local factories
- Strengthening their repair strategies
Which industries benefit most from spindle repair services?
Industries such as automotive, aerospace, electronics, and precision manufacturing heavily rely on spindle repair services. These sectors require their machinery to operate at peak performance to ensure quality production and uninterrupted workflow.