$193.08 Billion Expanding Aluminum Market in the U.S., China, and Germany by 2025
Explore the dynamic expansion of the global aluminum market, projected to reach $193.08 billion by 2025, with key insights into market growth across the U.S., China, and Germany. Discover industry trends, technological innovations, sustainability initiatives, and market challenges shaping the future of aluminum production and consumption in major economies.
- Last Updated:
Aluminum Market Q1 and Q2 2025 Forecast
The Aluminum market is expected to reach $193.08 billion in 2025, growing at a CAGR of 6.8% from 2025 to 2033. In Q1 2025, the market is forecasted to generate approximately $48 billion, driven by strong demand for lightweight materials in the automotive and aerospace industries in the U.S., China, and Germany. Aluminum continues to be favored for its strength-to-weight ratio, which is critical for improving fuel efficiency and performance in transportation and manufacturing sectors.
By Q2 2025, the market is expected to reach $49 billion, with substantial growth in China due to its large-scale infrastructure projects and sustainability initiatives aimed at reducing carbon emissions in the manufacturing processes.
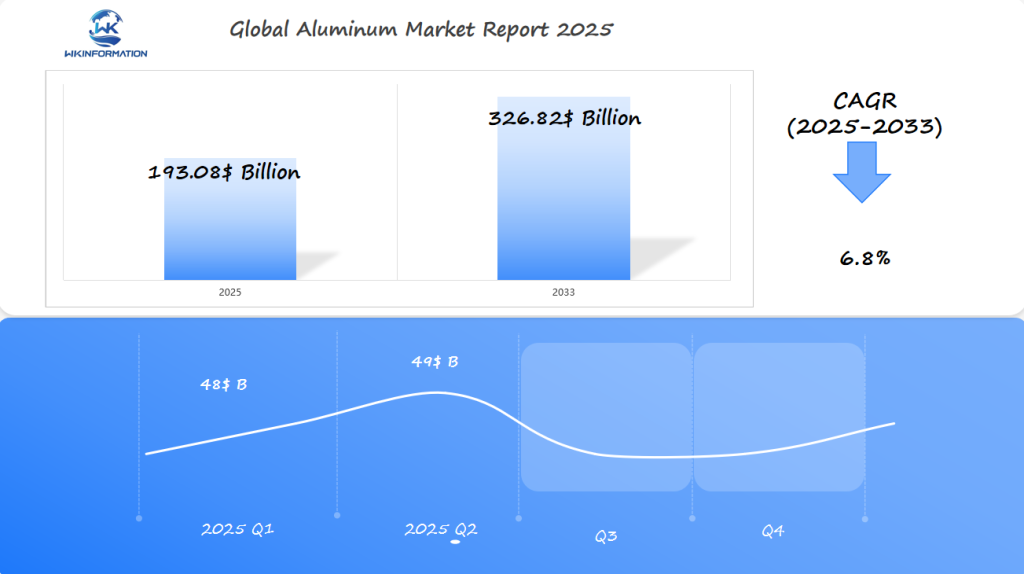
Exploring the Upstream and Downstream Industry Chains for Aluminum
The aluminum supply chain consists of two distinct segments: upstream and downstream operations, each playing a crucial role in the market’s efficiency and growth.
Upstream Operations
- Mining of bauxite ore
- Alumina refining through the Bayer process
- Primary aluminum production via electrolysis
- Raw material transportation and storage
Downstream Operations
- Secondary processing and fabrication
- Manufacturing of semi-finished products
- Production of end-user products
- Distribution to various industries
Major players dominate different segments of the supply chain:
- Mining Giants: Rio Tinto, Alcoa, BHP Billiton
- Primary Producers: Rusal, China Hongqiao Group
- Fabricators: Novelis, Constellium
- End-Product Manufacturers: Boeing, Ford, Saint-Gobain
Supply chain efficiency directly impacts market growth through:
- Cost reduction in transportation and storage
- Improved production scheduling
- Better inventory management
- Reduced lead times for delivery
Recent technological advancements have enhanced supply chain optimization:
- AI-powered demand forecasting
- Blockchain for transparency
- IoT sensors for real-time tracking
- Automated warehouse management systems
The integration of these technologies has resulted in a 15-20% improvement in supply chain efficiency, contributing to market expansion and reduced operational costs.
Key Trends in the Aluminum Market: Demand for Lightweight Materials and Recycling
The automotive industry’s shift toward lightweight materials has positioned aluminum as a critical component in vehicle manufacturing. Aluminum components reduce vehicle weight by up to 40% compared to traditional steel parts, directly translating to improved fuel efficiency and reduced emissions.
Key Benefits of Lightweight Aluminum in Automotive Applications:
- 5-7% fuel savings for every 10% reduction in vehicle weight
- Enhanced vehicle performance and handling
- Improved acceleration and braking capabilities
- Reduced CO2 emissions by up to 20%
The recycling landscape for aluminum presents compelling advantages for manufacturers and environmental initiatives:
Recycling Statistics and Impact:
- 75% of all aluminum ever produced remains in active use today
- Recycling aluminum requires only 5% of the energy needed for primary production
- Each ton of recycled aluminum saves approximately 9 tons of CO2 emissions
Market demand for recyclable materials continues to surge, driven by:
Consumer Preferences:
- Growing environmental awareness
- Increased focus on sustainable products
- Support for eco-friendly brands
Industry Requirements:
- Stringent environmental regulations
- Corporate sustainability targets
- Cost-effective production methods
The combination of lightweight properties and recycling potential has created a robust market for aluminum in sustainable manufacturing practices, particularly in electric vehicle production and green building initiatives.
Challenges in Aluminum Production: Environmental Impact and Energy Costs
Aluminum production faces significant environmental and cost-related challenges that shape the industry’s future. The extraction and processing of aluminum generate substantial greenhouse gas emissions, with each ton of aluminum produced releasing approximately 9-12 tons of CO2 into the atmosphere.
Key Environmental Challenges:
- Red mud waste production during bauxite refining
- High water consumption in processing
- Soil contamination near production facilities
- Air quality impacts from smelting operations
The energy-intensive nature of aluminum production creates a substantial cost burden for manufacturers. A typical aluminum smelter consumes about 14,500 kilowatt-hours (kWh) per ton of aluminum produced, making energy costs account for 30-40% of production expenses.
Regulatory Compliance Requirements:
- Carbon emission caps
- Waste management protocols
- Air quality standards
- Water usage restrictions
These environmental and energy challenges have prompted stricter regulations across major manufacturing regions. The U.S. Environmental Protection Agency enforces specific emission limits for aluminum production facilities, while the European Union’s emissions trading system impacts production costs through carbon pricing mechanisms.
The industry faces mounting pressure to adopt cleaner technologies and reduce its carbon footprint. Companies investing in energy-efficient smelting processes and renewable energy sources often encounter high initial capital requirements, affecting their competitive position in the global market.
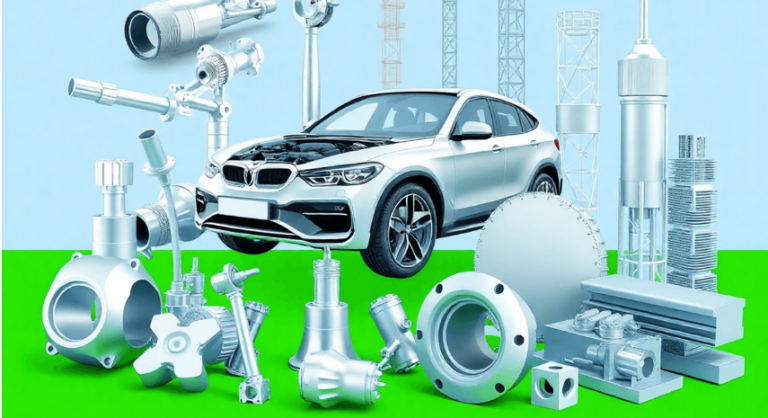
Geopolitical Impact on the Aluminum Market
The aluminum market’s dynamics shift significantly with changing international relations and trade policies. Recent years have witnessed substantial market volatility due to geopolitical tensions between major aluminum-producing nations.
Trade Agreement Impact:
- Regional trade pacts influence aluminum pricing structures
- Supply chain disruptions occur during policy changes
- Market access restrictions affect global availability
Tariff Effects on Production:
- Import duties raise manufacturing costs
- Production relocations to circumvent trade barriers
- Price fluctuations due to policy uncertainties
The implementation of Section 232 tariffs by the U.S. created ripple effects across global aluminum markets. Chinese producers faced additional scrutiny, leading to shifts in export patterns and domestic stockpiling. European manufacturers adapted their strategies to maintain market competitiveness amid changing trade landscapes.
Sanctions and Market Response:
- Supply chain diversification efforts
- Development of alternative sourcing routes
- Creation of regional manufacturing hubs
Trade tensions between major economies have prompted companies to reevaluate their supply chain strategies. The aluminum industry has seen the emergence of new trading partnerships and production centers as businesses adapt to evolving geopolitical realities. These changes have led to price volatility and altered traditional supply-demand relationships in key markets.
The establishment of new trade corridors and strategic partnerships continues to reshape the global aluminum landscape, influencing both pricing mechanisms and market accessibility.
Types of Aluminum: Primary, Secondary, and Alloyed
Primary Aluminum
Primary aluminum comes from the electrolysis of alumina, which is extracted directly from bauxite ore using the Hall-Héroult process. This raw material has high purity levels, making it perfect for specialized applications that require strict quality standards.
Secondary Aluminum
Secondary aluminum is made from recycled products and scrap materials. The production process includes:
- Sorting and cleaning of scrap
- Melting in rotary or reverberatory furnaces
- Refining and removal of impurities
- Casting into new forms
Alloyed Aluminum
Alloyed aluminum is created by combining pure aluminum with other elements to improve specific properties:
Common Aluminum Alloys:
- 2xxx series (Al-Cu): High strength, used in aircraft structures
- 3xxx series (Al-Mn): Improved formability, perfect for beverage cans
- 5xxx series (Al-Mg): Superior corrosion resistance, marine applications
- 6xxx series (Al-Mg-Si): Excellent extrudability, architectural components
- 7xxx series (Al-Zn): Maximum strength, aerospace applications
The choice between primary, secondary, or alloyed aluminum depends on the intended application. Primary aluminum is used for critical aerospace components, secondary aluminum is suitable for construction materials, while alloyed variants meet specific industry requirements for strength, durability, or corrosion resistance.
The production methods and applications continue to evolve as manufacturers develop new alloys and recycling technologies to meet changing market demands.
Applications of Aluminum in Automotive, Construction, and Aerospace Industries
Aluminum is widely used in various industries due to its versatility and durability. Here are some specific applications of aluminum in the automotive, construction, and aerospace sectors:
1. Automotive Industry
The automotive industry harnesses aluminum’s versatility across multiple vehicle components:
- Engine Components: Cylinder heads, engine blocks, pistons, transmission housings
- Body Structure: Hood panels, door frames, trunk lids, crash management systems
2. Construction Industry
In construction, aluminum’s durability creates lasting architectural solutions:
- Structural Elements: Curtain walls, window frames, roofing systems, support beams
- Interior Features: HVAC systems, lighting fixtures, decorative panels, suspended ceilings
3. Aerospace Industry
The aerospace sector relies on aluminum’s strength-to-weight ratio:
- Aircraft Components: Fuselage structures, wing components, landing gear parts, interior cabin elements
Recent innovations have expanded aluminum’s applications through advanced manufacturing techniques. The automotive sector now uses aluminum-intensive designs to reduce vehicle weight by up to 40%. Construction companies integrate aluminum composite materials for enhanced building performance. Aerospace manufacturers employ specialized aluminum alloys that withstand extreme temperatures and pressure conditions at high altitudes.
The demand for aluminum continues to grow as industries seek lightweight, durable materials. You’ll find aluminum components in electric vehicles, green buildings, and next-generation aircraft, highlighting its crucial role in modern industrial applications.
Global Insights into the Aluminum Market
The global aluminum market shows different regional trends and growth paths. Asia-Pacific is the largest player, holding 60% of the market share, mainly due to rapid industrialization and infrastructure development in countries like India and Southeast Asian nations.
Regional Market Distribution:
- Asia-Pacific: Leading with 60% market share
- North America: 20% market share
- Europe: 15% market share
- Rest of World: 5% market share
Growth Drivers by Region:
Asia-Pacific
- Expanding construction sector
- Rising automotive production
- Increased electronics manufacturing
North America
- Electric vehicle revolution
- Aerospace industry demands
- Sustainable packaging initiatives
Europe
- Green building regulations
- Automotive lightweighting requirements
- Renewable energy infrastructure
The market shows different consumption patterns in various regions. While Asia-Pacific focuses on large-scale production and infrastructure projects, North America prioritizes high-quality aluminum for specific uses. European demand is centered around sustainable and recycled aluminum products, reflecting strict environmental regulations.
Current market forecasts predict a compound annual growth rate of 5.8% until 2025, with emerging economies in Southeast Asia and Latin America offering new growth opportunities. Changing trade dynamics and regional manufacturing capabilities continue to reshape global aluminum supply chains.
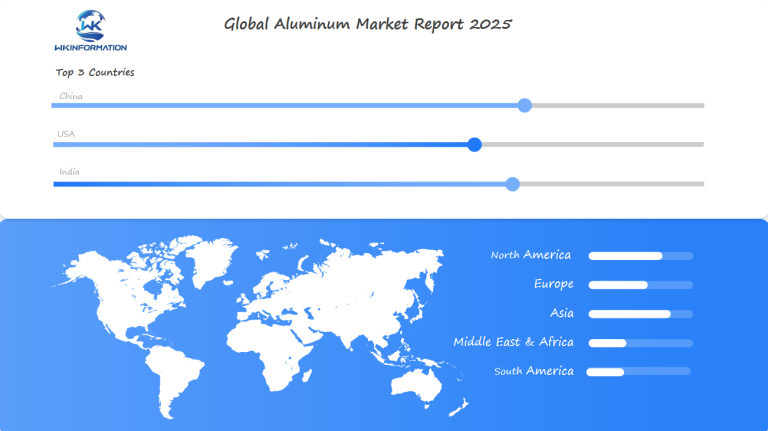
U.S. Aluminum Market: Growth in Automotive and Aerospace Industries
The U.S. aluminum market is experiencing significant growth, particularly in the automotive and aerospace industries. American car manufacturers are increasingly using aluminum as a key material for their upcoming vehicles, with Ford’s F-150 truck line being a prime example of successful aluminum integration.
Key Automotive Applications:
- Engine blocks and cylinder heads
- Body panels and structural components
- Suspension systems
- Heat exchangers and radiators
The shift towards electric vehicles in the U.S. automotive industry has led to a higher demand for aluminum. Tesla, for instance, relies heavily on aluminum in its manufacturing processes to create lightweight vehicle frames without compromising strength.
Aerospace Sector Innovations:
- Advanced aluminum alloys in aircraft fuselage
- Lightweight components for satellite systems
- Specialized materials for defense applications
Boeing’s ongoing commitment to using aluminum in the production of commercial aircraft is also contributing to market growth. The company’s 737 MAX series features advanced aluminum alloys that result in up to 20% less fuel consumption compared to conventional materials.
U.S. manufacturers have developed proprietary aluminum alloys specifically designed for use in aerospace applications. These innovations include high-strength materials that can withstand extreme temperatures and resist corrosion, both of which are crucial for the performance of modern aircraft.
The U.S. Department of Defense’s ongoing efforts to modernize its military capabilities are creating additional demand for specialized aluminum products, particularly in the development of military aircraft and spacecraft. This strategic focus further solidifies the United States’ position as a leader in aerospace-grade aluminum applications.
China's Aluminum Market: Production Capacity and Export Dynamics
China is the world’s leading producer of aluminum, accounting for over 50% of global supply. The country’s production capacity has reached unprecedented levels, driven by:
- Advanced Manufacturing Infrastructure
- Lower Production Costs
- Substantial Government Support
- Abundant Raw Material Access
Competitive Advantages of Chinese Manufacturers
Chinese manufacturers maintain competitive advantages through strategic investments in automation and scale economies. Their production facilities operate 24/7, utilizing cutting-edge technology to maximize output efficiency.
Impact of Domestic Policies on Export Dynamics
The country’s domestic policies significantly shape export dynamics. Recent environmental regulations have prompted manufacturers to adopt cleaner production methods, impacting output levels. Despite these challenges, Chinese exports continue to grow, supported by:
- State-backed financing options
- Streamlined logistics networks
- Integrated supply chains
- Strategic partnerships with global buyers
Cost Advantages through Vertical Integration
Chinese aluminum producers leverage cost advantages through:
Ongoing Expansion in the Market
The market sees ongoing expansion through:
- Technology Upgrades: Implementation of smart manufacturing systems
- Capacity Optimization: Strategic facility locations near raw materials
- Quality Control: Enhanced testing and certification processes
- Export Infrastructure: Improved port facilities and shipping networks
Adaptability of Chinese Manufacturers
Chinese manufacturers adapt quickly to market demands, adjusting production volumes and specifications to meet international standards while maintaining cost competitiveness.
Germany's Aluminum Market: Role in Industry 4.0 and Green Technologies
Germany’s aluminum industry is leading the way in technological innovation by embracing Industry 4.0. German manufacturers are implementing smart factory solutions such as:
- AI-powered quality control systems
- IoT sensors for real-time production monitoring
- Digital twin technology for process optimization
- Automated material handling systems
The country’s dedication to green technology initiatives has also revolutionized traditional aluminum production methods. German facilities are now using:
- Smart grid systems for efficient energy management
- Renewable energy sources in smelting processes
- Advanced recycling technologies that achieve 98% material recovery rates
- Zero-waste manufacturing practices
These advancements in technology have established German aluminum producers as leaders in sustainable manufacturing. The adoption of smart manufacturing solutions has led to significant improvements, including:
- 25% reduction in energy consumption
- 30% decrease in carbon emissions
- 40% increase in production efficiency
- 15% rise in recycling rates
German aluminum manufacturers are also utilizing data analytics to optimize production schedules and maintain quality standards. By integrating predictive maintenance systems, they can minimize downtime by identifying potential equipment failures before they happen.
The aluminum sector in Germany receives strong support from the government through initiatives like the National Industrial Strategy 2030, which promotes sustainable manufacturing practices and encourages technological innovation in metal production.
The Future of Aluminum: Sustainable Production and Recycling Initiatives
The aluminum industry is on the verge of significant changes driven by sustainable practices and innovative recycling technologies. Several groundbreaking initiatives are reshaping production methods:
Zero-Carbon Smelting
- Implementation of inert anode technology
- Carbon-free production processes
- Renewable energy integration in manufacturing
Advanced Recycling Technologies
- AI-powered sorting systems
- Automated scrap processing
- Enhanced purification methods for recycled materials
The industry’s commitment to sustainability extends beyond production. Digital tracking systems now monitor aluminum throughout its lifecycle, enabling precise recycling and reuse strategies. These technologies help maintain material quality across multiple recycling cycles.
Supply Chain Innovations
- Blockchain-based material tracking
- Smart contracts for recycling programs
- Decentralized collection networks
Research indicates a potential 40% reduction in production emissions by 2030 through these initiatives. Companies are investing in closed-loop systems where aluminum products are designed for easy disassembly and recycling.
Emerging Technologies
- Solar-powered smelting facilities
- Hydrogen-based reduction processes
- Bio-based alternatives for traditional chemicals
These advancements signal a shift toward circular economy principles, with manufacturers adopting design-for-recycling approaches. The integration of these sustainable practices is creating new opportunities for innovation while addressing environmental concerns in aluminum production.
Competitive Landscape in the Aluminum Market
The global aluminum market is characterized by the dominance of several key players and is influenced by factors such as production capacity, technological advancements, and geopolitical developments.
-
China Hongqiao Group – China
-
Alcoa Corporation – United States
-
Rio Tinto – United Kingdom / Australia
-
Rusal (UC Rusal) – Russia
-
Norsk Hydro ASA – Norway
-
China Power Investment Corporation (CPI) – China
-
Chalco (Aluminum Corporation of China) – China
-
Emirates Global Aluminium (EGA) – United Arab Emirates
-
Vedanta Limited – India
Overall
Report Metric | Details |
---|---|
Report Name | Global Aluminum Market Report |
Base Year | 2024 |
Segment by Type |
· Primary · Secondary · Alloyed |
Segment by Application |
· Automotive Industry · Construction Industry · Aerospace Industry |
Geographies Covered |
· North America (United States, Canada) · Europe (Germany, France, UK, Italy, Russia) · Asia-Pacific (China, Japan, South Korea, Taiwan) · Southeast Asia (India) · Latin America (Mexico, Brazil) |
Forecast units | USD million in value |
Report coverage | Revenue and volume forecast, company share, competitive landscape, growth factors and trends |
The aluminum industry stands at a pivotal crossroads where sustainability meets innovation. Forward-thinking companies that prioritize eco-friendly technologies and embrace circular economy principles are positioning themselves for sustainable long-term growth. Significant opportunities exist across diverse sectors, particularly in the expanding electric vehicle market, the growing aerospace industry, and the robust demands of the construction sector. The industry’s future success will be determined by how well companies adapt to these evolving market dynamics while maintaining a strong commitment to environmental stewardship and technological advancement.
Global Aluminum Market Report (Can Read by Free sample) – Table of Contents
Chapter 1: Aluminum Market Analysis Overview
- Competitive Forces Analysis (Porter’s Five Forces)
- Strategic Growth Assessment (Ansoff Matrix)
- Industry Value Chain Insights
- Regional Trends and Key Market Drivers
- AluminumMarket Segmentation Overview
Chapter 2: Competitive Landscape
- Global Aluminumplayers and Regional Insights
- Key Players and Market Share Analysis
- Sales Trends of Leading Companies
- Year-on-Year Performance Insights
- Competitive Strategies and Market Positioning
- Key Differentiators and Strategic Moves
Chapter 3: Aluminum Market Segmentation Analysis
- Key Data and Visual Insights
- Trends, Growth Rates, and Drivers
- Segment Dynamics and Insights
- Detailed Market Analysis by Segment
Chapter 4: Regional Market Performance
- Consumer Trends by Region
- Historical Data and Growth Forecasts
- Regional Growth Factors
- Economic, Demographic, and Technological Impacts
- Challenges and Opportunities in Key Regions
- Regional Trends and Market Shifts
- Key Cities and High-Demand Areas
Chapter 5: Aluminum Emerging and Untapped Markets
- Growth Potential in Secondary Regions
- Trends, Challenges, and Opportunities
Chapter 6: Product and Application Segmentation
- Product Types and Innovation Trends
- Application-Based Market Insights
Chapter 7: Aluminum Consumer Insights
- Demographics and Buying Behaviors
- Target Audience Profiles
Chapter 8: Key Findings and Recommendations
- Summary ofAluminumMarket Insights
- Actionable Recommendations for Stakeholders
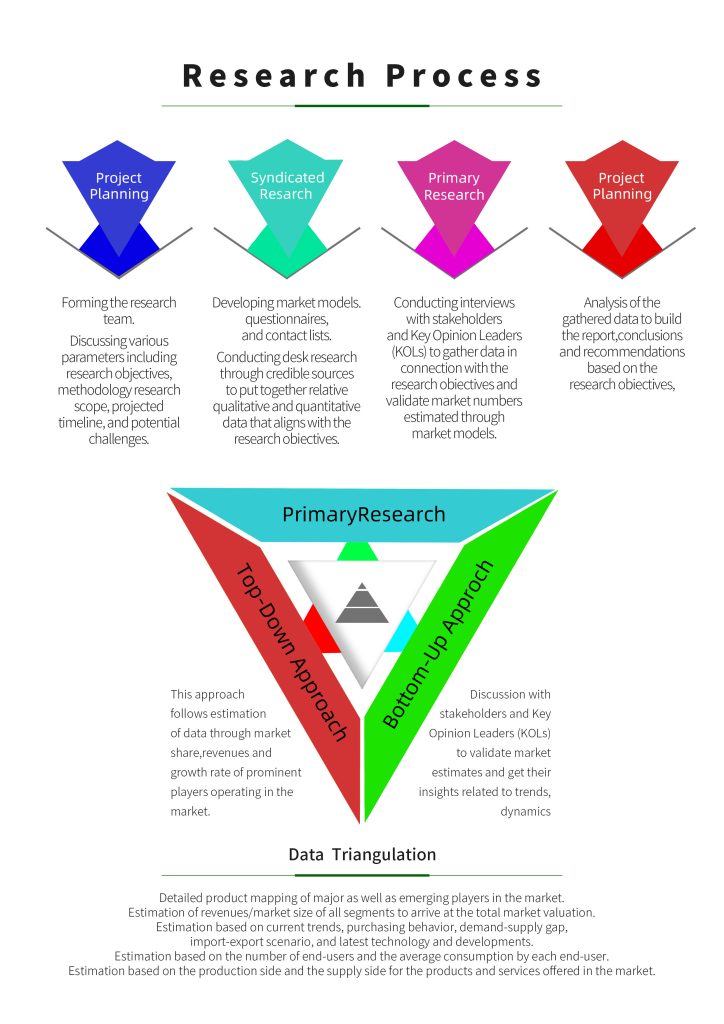
Access the study in MULTIPLEFORMATS
Didn’t find what you’re looking for?
TALK TO OUR ANALYST TEAM
Need something within your budget?
NO WORRIES! WE GOT YOU COVERED!
Call us on: +1-866-739-3133
Email: infor@wkinformation.com
What is the projected growth of the aluminum market by 2025?
The aluminum market is projected to expand to $193.08 billion by 2025, driven by significant growth in key regions such as the U.S., China, and Germany.
How do upstream and downstream processes influence the aluminum supply chain?
Upstream processes involve raw material extraction and initial processing, while downstream processes focus on manufacturing and distribution. The efficiency of these supply chain stages significantly impacts overall market growth and production viability.
What are the key trends driving demand for aluminum in various industries?
Key trends include the increasing demand for lightweight materials in the automotive sector to enhance fuel efficiency and a growing focus on recycling initiatives due to sustainability goals.
What environmental challenges does aluminum production face?
Aluminum production faces significant environmental challenges, including high energy consumption, regulatory pressures on emissions, and concerns regarding its overall environmental impact.
How do geopolitical factors affect the aluminum market?
Geopolitical factors such as international trade agreements, tariffs, and sanctions can influence aluminum prices, availability, and overall market dynamics.
What are the different types of aluminum used in various applications?
There are three main types of aluminum: primary aluminum (extracted from bauxite), secondary aluminum (recycled), and alloyed aluminum (mixed with other metals). Each type has specific applications across industries like automotive, construction, and aerospace.